Żadna z dotychczas znanych i stosowanych technologii bezwykopowych nie oferuje tak wielu korzyści jak nasza zaawansowana technologia instalacji grawitacyjnych. W przypadku skomplikowanych i wymagających projektów instalacji podziemnych, nasza Wiertnica Grawitacyjna jest niezastąpiona, zapewniając najwyższą precyzję i skuteczność.
Kluczowe zalety technologii Wierceń Grawitacyjnych:
- Minimalna ingerencja w infrastrukturę: Nasza technologia pozwala na realizację przewiertów z typowych studni kanalizacyjnych (DN 1000, DN 1200 i większe) bez konieczności ingerencji w istniejącą zabudowę czy nawierzchnię.
- Brak konieczności wykopów: Wszystkie prace zaczynają się i kończą w studni, eliminując potrzebę wykonywania dodatkowych komór startowych.
- Wszechstronność technologii: Możliwość montażu w studniach o dowolnym kształcie lub w niestandardowych warunkach, np. przy ograniczonej przestrzeni lub niskiej wytrzymałości mechanicznej.
- Przewierty na każdej głębokości: Nasza technologia umożliwia wiercenie poniżej poziomu wody gruntowej na całej trasie przewiertu, co czyni ją idealnym rozwiązaniem dla skomplikowanych gruntów.
- Precyzja i dokładność: Kanały wykonywane są z dokładnością do 2‰, niezależnie od klasy gruntu (piaski, żwiry, gliny, a nawet skały miękkie i średnie).
Nasza technologia to doskonały przykład zastosowania przewiertów sterowanych HDD i mikrotunelowania, które cieszą się coraz większą popularnością wśród inwestorów ze względu na ich ekologiczność i minimalny wpływ na otoczenie. Podczas realizacji instalacji kanalizacyjnych, instalacje podziemne bez wykopów stają się kluczowym rozwiązaniem w terenach o gęstej zabudowie miejskiej.
Technologia podwójnego napędu
Rozwiązanie, które wyróżnia naszą Wiertnicę Grawitacyjną, to system podwójnego napędu, umożliwiający efektywne przewiercanie się przez gruz, głazy, przeszkody betonowe i inne trudne warunki gruntowe bez utraty precyzji.
Zalety naszej technologii w praktyce:
- Brak konieczności blokowania ścieków podczas prac w czynnych kolektorach.
- Technologia zwiększa zagęszczenie gruntu wokół układanej rury, co wzmacnia strukturę podłoża.
- Możliwość pracy w wymagających środowiskach bez dodatkowych prac adaptacyjnych.
Dzięki naszej technologii osiągamy wyższą efektywność i oszczędności w porównaniu z innymi metodami bezwykopowymi. Przewierty sterowane i nasza innowacyjna wiertnica to odpowiedź na rosnące potrzeby rynku, łącząc precyzję z uniwersalnością zastosowań.
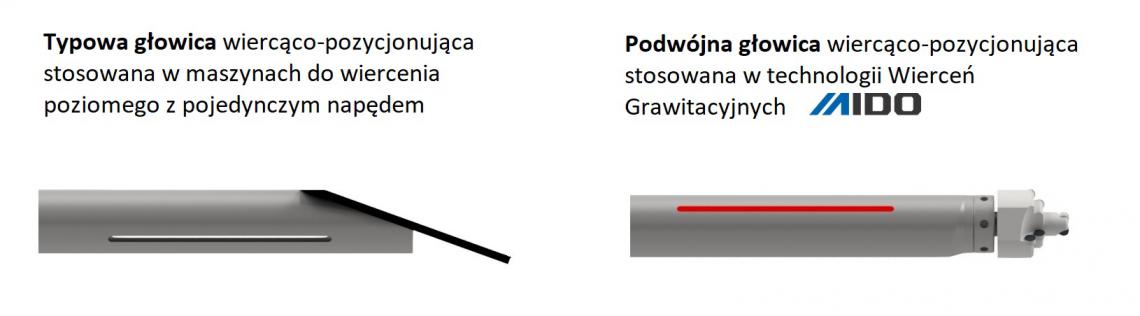
W większości technologii i maszyn przeznaczonych do wierceń poziomych, np. wiertnice HDD, stosowane są pojedyncze napędy współpracujące z pojedynczymi głowicami wiercącymi. Taka pojedyncza głowica zawiera w sobie jednocześnie elementy skrawające oraz elementy pozycjonujące głowicę. Taka głowica posiada wyłącznie jeden napęd obrotowy realizujący jednocześnie wiercenie w gruncie oraz umożliwiający sterowanie kierunkiem przewiertu. W typowych gruntach, pozbawionych dużych i twardych frakcji, typowa głowica poradzi sobie z realizacją przewiertu, bez utraty zadanego kierunku. Problem pojawi się, gdy podczas wykonywania przewiertu pilotażowego, napotkamy na twardą przeszkodę. Pojedyncza głowica z pojedynczym napędem będzie miała trudność z przewierceniem się przez taką przeszkodę i albo w ogóle nie uda się jej tej przeszkody przewiercić, albo pokona ją utraciwszy zadany kierunek wiercenia. Głowica zawierająca w sobie zarówno elementy odpowiedzialne za wiercenie jak i sterowanie, nie posiada pełnych i skutecznych właściwości wiercących. Schemat takiego działania zilustrowano poniżej.
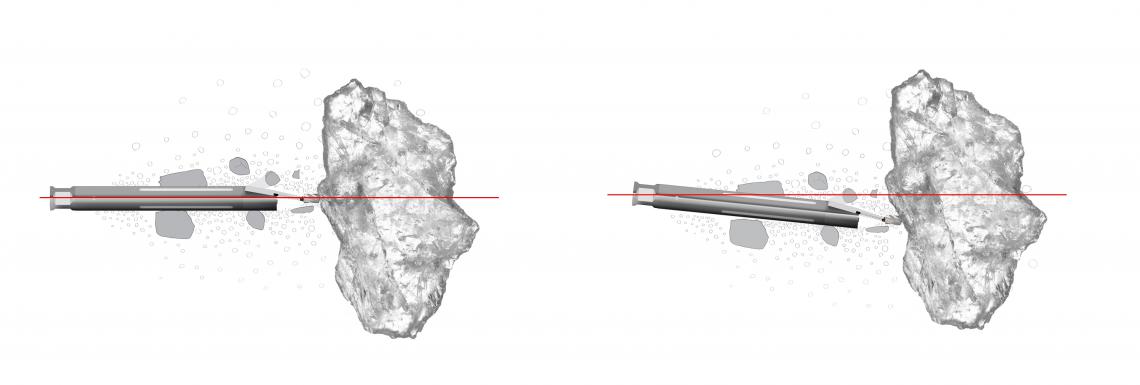
Efektem zmiany kierunku wiercenia będzie zmiana planowanego i wymaganego spadku grawitacyjnego wykonywanej instalacji, co zazwyczaj wyklucza pozytywny odbiór wykonanej pracy przez zleceniodawcę/inwestora. W skrajnej sytuacji nie uda się pokonać przeszkody.
Rozwiązanie tego problemu jest zastosowanie urządzenia posiadającego napęd podwójny, czyli dwa niezależne napędy głowicy. W naszej technologii Wierceń Grawitacyjnych zastosowaliśmy nasz innowacyjny system podwójnego napędu, w którym jeden napęd jest odpowiedzialny za wiercenie w gruncie, a drugim napędem realizujemy sterowanie kierunkiem przewiertu. Dzięki temu kształt i funkcjonalność głowicy wiercącej mogą być w pełni zorientowane na pokonywanie wszelkich napotkanych przeszkód, co zapewnia pełną skuteczność w pokonywaniu niemal wszystkich przeszkód. Poniższa ilustracja obrazuje schematycznie rozwiązanie podwójnego napędu głowicy.
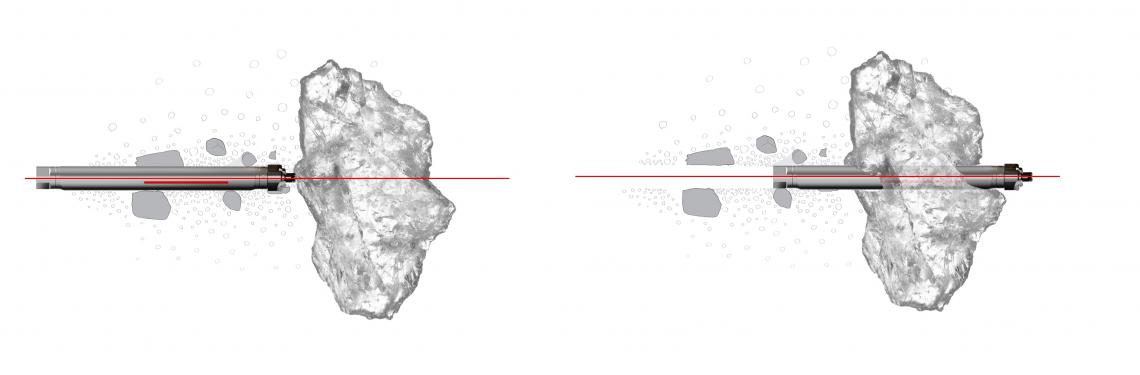
Zastosowanie podwójnego napędu pozwala na pokonywanie niemal wszystkich przeszkód występujących w gruncie, bez ryzyka utraty zadanego kierunku. Możemy mieć pewność, że wykonana instalacja będzie miała zadany i precyzyjny spadek grawitacyjny.
W PEŁNI BEZWYKOPOWO W KAŻDYCH WARUNKACH
Bardzo często mamy do czynienia z sytuacją, gdy inny potencjalny wykonawca instalacji, po wizji lokalnej na budowie będącej obszarem prac, rezygnuje z podjęcia się budowy. Powodem jest zazwyczaj brak możliwości zainstalowania się z maszynami, z uwagi na ograniczoną ilość miejsca. Wszelkie inne urządzenia bezwykopowe, precyzyjne wiertnice lub przeciskarki, wymagają wykonania dużych komór roboczych, co wiązałoby się z koniecznością wyłączania z ruchu całych ciągów komunikacyjnych. My, do pracy przy udziale naszej technologii wierceń sterowanych, potrzebujemy jedynie samej studni startowej, DN1000, DN 1200 lub DN1500, lub obszaru/komory o wielkości takich studni, by zainstalować nasze urządzenie bezpośrednio w studni lub w komorze, poprzez zastosowanie odpowiedniego adaptera.