We are pleased to announce that during the 8th International Conference on Trenchless Technologies NO-DIG POLAND 2018, the technology of horizontal precise steered drilling we use, won the recognition of the international jury by awarding it a distinction.
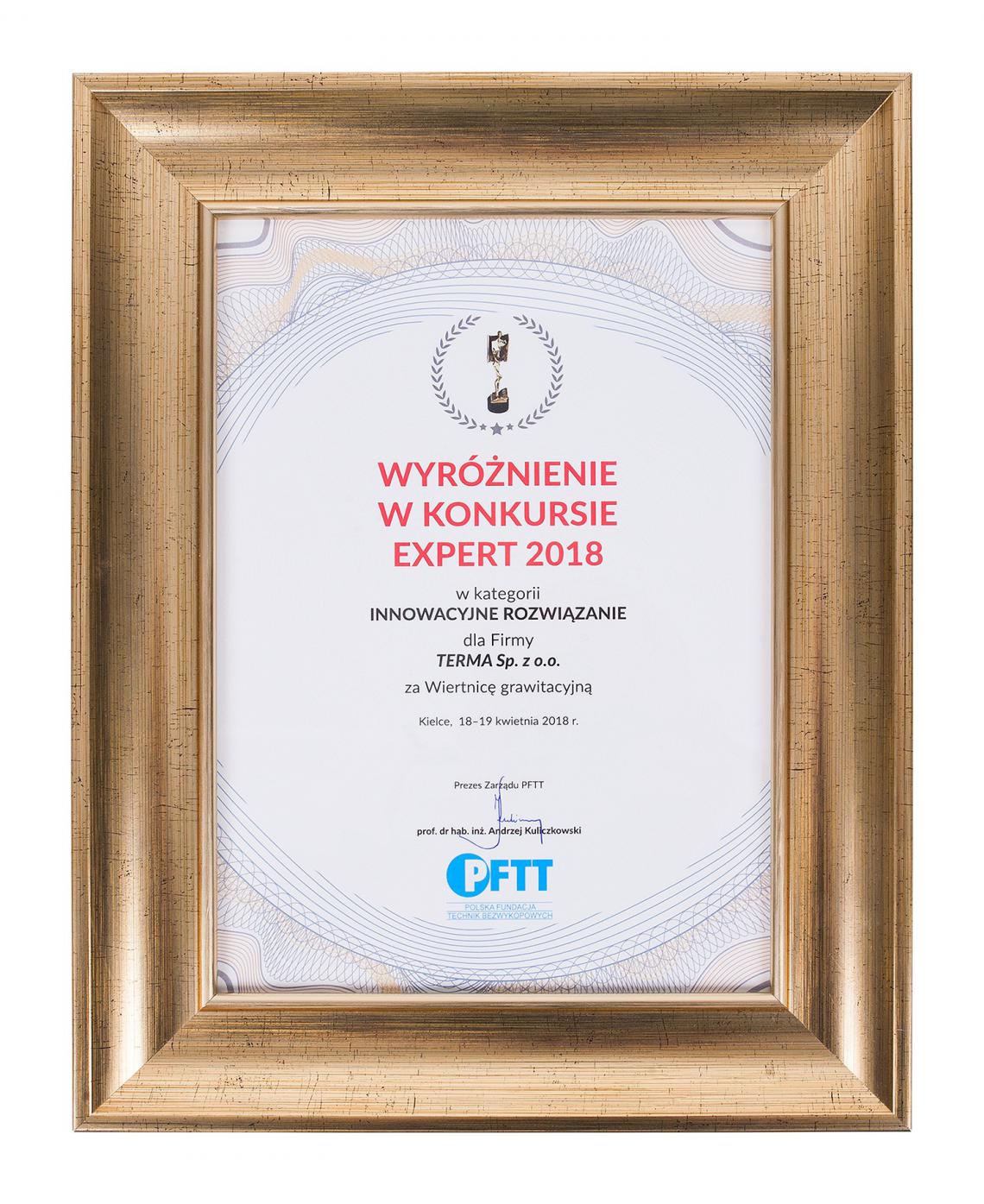
Developed by Terma Sp. z o.o. and the Gravity Drilling Technology we use, is a highly innovative device for gravity installations - sewage and rainwater systems, which require exceptional precision of the set gradient of the installation. The device was created as a response to the market requirements for trenchless installations. Unfortunately, these requirements were not met by any device and any technology available on the market. This technology allows for the implementation of almost any installation using the trenchless method, regardless of ground conditions and regardless of the building conditions around the planned installation. It also allows for the renovation of existing channels and for pulling casing pipes into heating installations with high precision.
The elements that distinguish our solution from the technologies available on the market are:
- installation from the starting well to the final well, without any interference with the existing infrastructure, without any additional excavations. Work begins in the well and ends in the well. Installations are made from wells DN 1200 or larger. The design of the machine allows it to be inserted through a typical DN 600 manhole
- performing installations at groundwater depths or at significant depths, up to 15 meters (it is possible to perform installations at much greater depths, although we have not met with such depths so far)
- the drilling machine can be operated directly at the bottom of the well (in new wells) or directly from the base plate, without the need to completely disassemble the landing or to trim the well
- the drilling machine can work directly under the cover of the well or space-limiting elements, such as reduction rings, reducers, etc., without the need to disassemble them
- performing gravity installations within a very narrow tolerance range of up to 0.2%
- construction of an installation from a starting well with low mechanical strength
- installation without blocking the flow of sewage
- work in soils with drilling classes: II, III, IV, V (sand, gravel, clay and soft rocks, medium: marly limestones, order clay, marls, sand shales, rubble, concrete obstacles)
- the possibility of post-construction correction of the installation and getting rid of local shortcomings of straightness
- reduction of the impact on the surrounding natural environment as a result of not interfering with the surrounding groundwater (no need for dehydration, which deprives the soil of microorganisms and changes its structure)
- no reduction in compaction, our solution allows you to even thicken the zone around the pipe to be laid and around the well (the excavated material is mostly reamed and pushed, a small amount is removed from the borehole)
- ensuring the improvement of work safety in terms of the successful implementation of the installation. Other technologies, such as microtunnelling technology, are associated with the risk of installation failure and, moreover, high costs associated with damage to the drilling machine itself. It happens when we encounter hard obstacles such as boulders or empty chambers along the route of the installation
- simplification of the estimation of installation costs depending on the difficulties, both known to us before starting the task, and those unexpected, resulting from the work - dealing with any obstacle, such as a pebble or an empty chamber, requires repeatable procedures based on the same activities and materials
- reduction of installation time, depending on the installation depth and difficulty, in the range of 20 - 50%. For our technology, there is no need to build starting chambers and drain them, which is the case with the use of larger and heavier machines, and to place them in these chambers. This saves us time up to several hours, which is half of the time spent on the installation. Drilling itself takes a comparable amount of time.