This presentation of popular trenchless technologies has been made mainly in order to compare the possibilities and application in the implementation of the most demanding projects, such as underground gravity installations. The difficulties associated with their implementation result from the need to build an installation with a specific, often very precise gravitational drop. Very often, such installations are built in a very densely built-up area, where there is no place to install a larger machine. Often we are dealing with a project of making underground pipe connections between the existing sewage chambers. Their partial dismantling in order to install machines for the construction of the installation, due to the accompanying communication difficulties, creates limitations or even prevents the use of some of the technologies described later. In our comparison, we want to show how many benefits come from the use of the trenchless technology of Gravity Drilling, especially in the most demanding projects - gravity installations.
Excavation - the easiest way?
By observing the projects related to the construction of all underground installations, it can be concluded that the most popular technology is still the excavation of an open trench. This method seems to be the simplest and most effective. How such an implementation looks like in a nutshell: we make an excavation along the entire length of the installation, and in places of connections or existing wells. Then, we place the installation in the trench and backfill it, compacting every given layer of backfill. Then you still need to restore the condition of the surface: asphalt, paving stones or other. Overall, it is a very costly and, above all, time-consuming process. Speaking of costs, it is worth adding the so-called social costs, related not so much to the physical implementation of the construction itself, but to the costs resulting from the inconvenience of this construction for the local society. The existing road infrastructure, located directly at the construction site and adjacent to it, must be excluded from use for the entire duration of the works. This is associated with serious communication difficulties, the need to organize detours. Time wasted in traffic jams, wasted fuel are a large amount of additional costs that are usually not included in the overall calculation of investment costs.
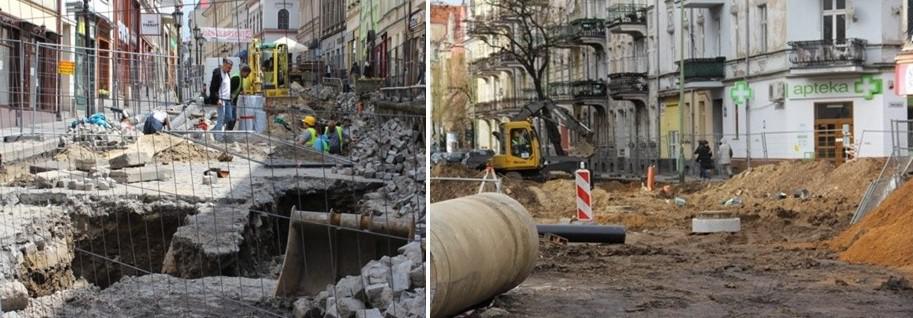
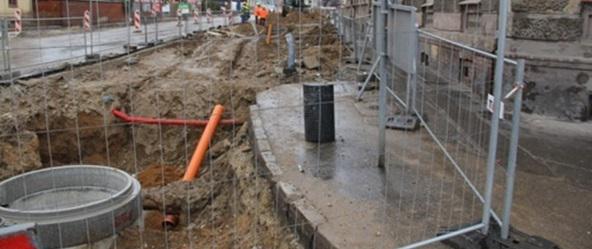
It is also worth mentioning the costs associated with environmental pollution, both through the machines involved in the excavation of the installation, and the emission of exhaust gases caused by communication difficulties. With the open excavation technology, practically any type of installation can be realized, including precise gravity installations. However, the costs of such installations, both direct and high social costs, related to communication difficulties and the necessity to completely exclude the entire area of works from operation, put this technology into great doubt.
SUMMARY OF EXTRACTION TECHNOLOGY:
- Still a frequently used technology, despite the possibility of using trenchless technologies.
- It generates high direct and social costs and large communication difficulties.
- Justified only for the construction of new installations with the simultaneous construction of new or renovation of existing pavements.
- Large communication difficulties throughout the construction area.
Ground Rockets (Moles) - the simplest trenchless solutions
The simplest trenchless technology is the construction of installations using Ground Rockets, commonly known as Moles. The mole is a simple and cheap, but at the same time very effective device that allows you to perform all types of installations: energy, gas, teleinformation, energy and water and sewage.
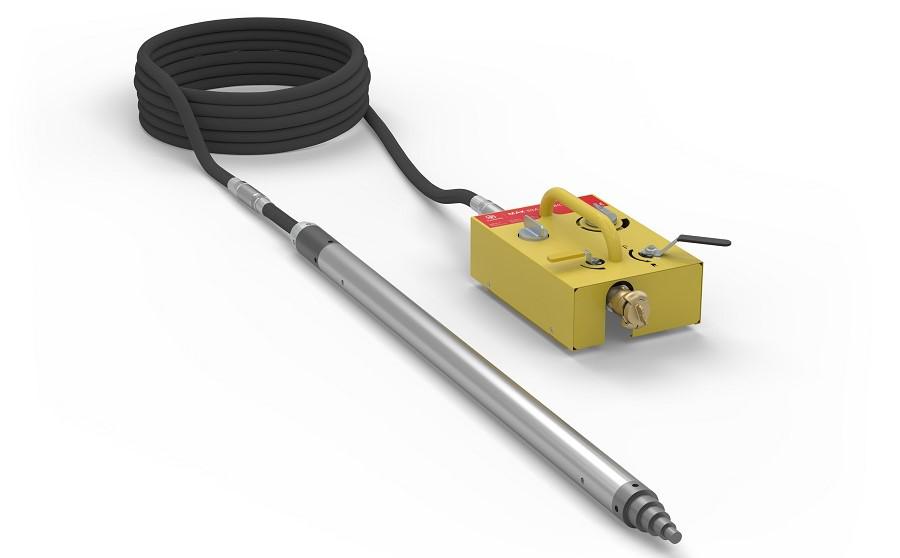
To perform the installation with a mole, it is necessary to make a starting and, most often, final excavation, although the latter is not necessary in most cases.
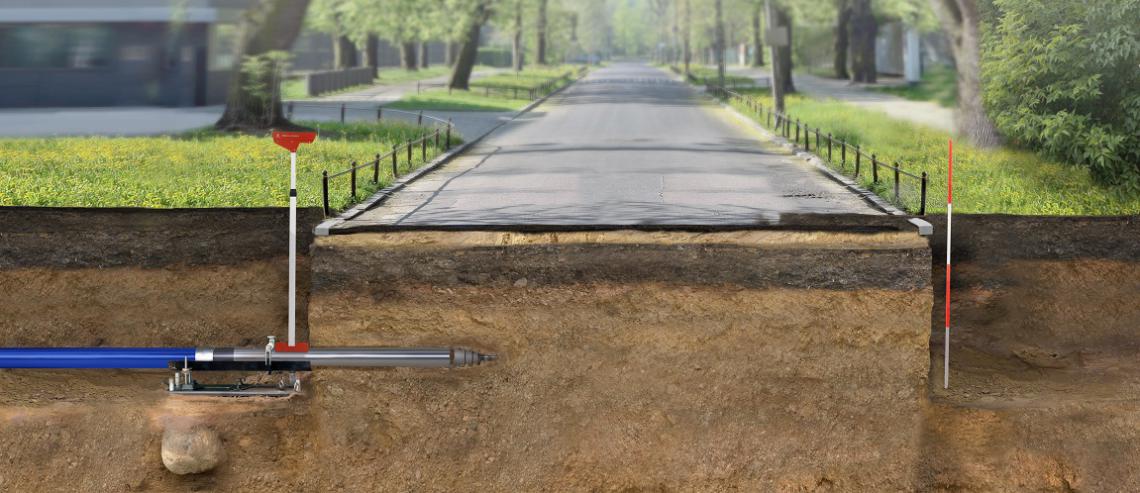
The mole is an unmanaged device. It is only possible to change the direction of work front-back. These features, however, do not limit the performance of typical installations for which moles are intended: short, usually up to twenty meters long installations at the intersection / passage of the installation under the local communication route. A good, accurate mole, in the hands of an operator with minimal experience, will perform such an installation with due accuracy and care. The mole performs the installation by pushing itself into the ground and pushing it around itself as it moves forward. Most often, a pipe is installed directly behind the mole.
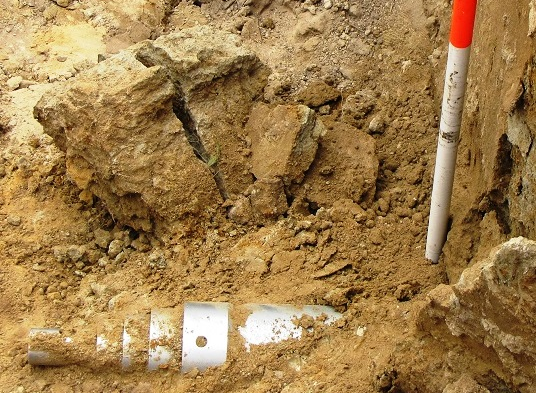
With the use of a mole, it is easy to make typical pressure installations or any other installations that do not require a precise slope, such as: water or gas connections, all teletechnical and energy installations. The problem will arise when we need to make gravity installations that require a precise slope. We cannot steer the mole during the installation, both horizontally and vertically. The precision of the installation with a mole depends on how precisely we manage to direct it in the initial phase of jacking. It also depends on ground conditions and our experience in making installations using a mole. When a mole encounters a hard obstacle, it may slightly change its direction. We will not be able to correct this direction, because, as mentioned, the mole is a device without the possibility of controlling it in the vertical and horizontal plane during operation. As a result of a change of direction at the moment of encountering a hard obstacle, the destination point of the installation under construction will change. This deviation will be slight, from a few to several dozen centimeters. However, it may be so important that we will not achieve the set, precise gravitational drop along the entire length of the installation. Such a precise slope is required in the construction of gravity installations, such as, for example, very precise sewage connections or sewage collectors. For such installations, a mole will not be a good and effective trenchless solution. However, this does not mean that moles are completely useless for the construction of gravity installations. Moles, well-designed in terms of accuracy, are quite often used in the case of making short gravity sewer connections, reaching several meters, where we have a large, up to several percent tolerance margin for making a drop. At a short distance, the slight deviation of the mole boring the hole in the ground has little effect on the overall installation and enables the final achievement of the required gravitational drop, within the range of a few percent required by the designer and network assumptions.
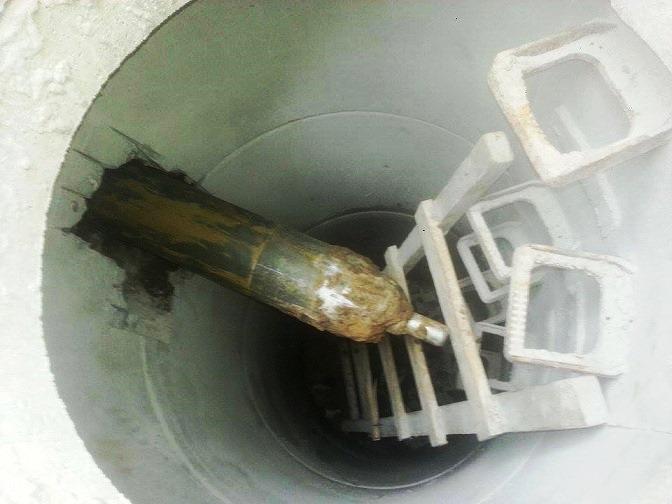
However, when the tolerance of the installation is much smaller, as is the case, for example, in the case of building a network of sewage collectors, where we are talking about the tolerance of decline measured in per mille, the use of a mole will involve a high risk of not achieving the precision specified by the network design. We definitely do not recommend moles for installations requiring high precision in maintaining the assumed gravity drop. Moreover, the mole is not suitable for installation between existing manholes, e.g. typical DN 1200 manholes, due to its length. We will not fit a mole in such a well without having to partially disassemble it. Using a mole, you can only install pipes with diameters up to a maximum of 180-200 mm. The use of moles for installations longer than 20, maximum 30 meters is also debatable.
SUMMARY OF MOLES TECHNOLOGY:
- The technology is definitely better than the excavation method, when used for short installations running under the existing road infrastructure.
- The technology is very effective for installations that do not require high precision.
- Significant reduction of the time and costs of implementation in relation to excavation technologies.
- No communication difficulties or interference with the existing infrastructure.
- Possibility of making gravity connections at short distances and with the required low precision of the slope.
- No possibility of trenchless installation between the existing sewage chambers.
- Limited installation length and diameter of installed pipes.
Non-steerable hydraulic jacking machines
An alternative for simple and non-steerable Moles are hydraulic jacking machines. It should be noted that to compare them with moles, we take into account simple hydraulic machines, without the possibility of controlling the jacking trajectory during the work.

The capabilities of such a device are similar to those of the mole, although the mole will certainly be more effective and accurate, and the installation with a mole will be less time-consuming and easier, less absorbing the operator of the machine. The Hydraulic Jacking Machine will not do as well as a mole, in soils with many hard obstacles. The accuracy of the jacking made in such soils will be much higher in the case of moles, due to the dynamic form of implementation (stroke) and the shape of the head enabling the neutralization / overcoming obstacles. Installations made with the use of Hydraulic Jacks are used on the market similar to moles. With this technology, you can also make simple gas, IT and energetical installations, and other pressure installations which do not require high precision of gravity drop. Due to the lower efficiency in overcoming obstacles and accuracy than in the case of moles, especially in more difficult and harder soils, simple and typical installations are most often made with the use of moles. The construction of even the shortest and not requiring high precision gravity connections should be done with at least moles. However, it is best to use more advanced technologies, described later in this article. The maximum lengths of jacking and installed pipe diameters in the case of Hydraulic Jacking Machines are similar like for Moles.
SUMMARY OF THE NON-STEERABLE HYDRAULIC JACKING MACHINES:
- The technology is definitely better than the excavation method, for making short installations running under the existing road infrastructure.
- Low accuracy limiting this technology to making installations on short distances and not requiring precision.
- No communication difficulties or interference with the existing infrastructure.
- It is not recommended for any gravity installations requiring a imposed drop.
- No possibility of fully trenchless installation between existing sewage chambers.
- Limited jacking length and installed pipe diameter.
Steerable hydraulic jacking machines
Devices very similar in terms of functionality, possibilities and application to the one described in the previous section. The distinguishing feature is the ability to control the jacking direction on an ongoing basis during the installation, which, combined with the jacking head location system, gives the system operator control over jacking correctness in terms of accuracy, keeping the set trajectory and the set gravitational drop. However, these machines have not met with great popularity on the market in use.
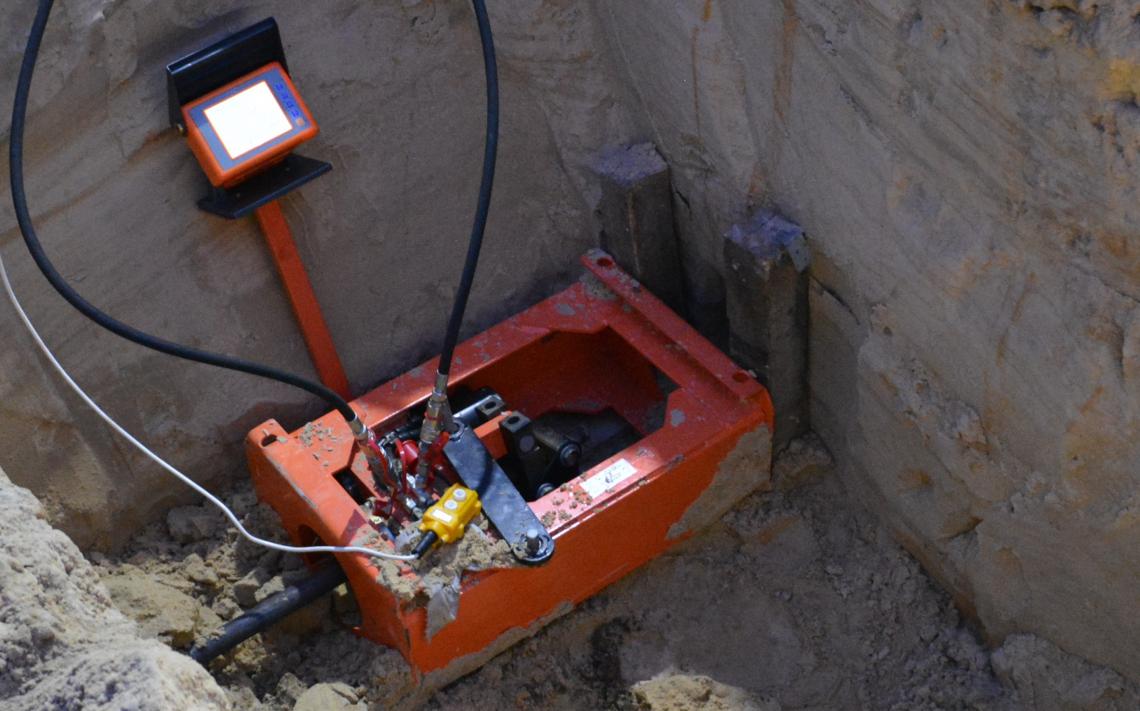
Although they have the ability to control the direction of jacking, their very ability to move the head in the ground and overcome obstacles, even in conjunction with the controllability of the jacking, does not allow for precise installations, especially over longer distances. Making very precise gravity installations is completely out of the range for this technology. The head, encountering a hard obstacle, is not able to overcome it without losing the given direction and the given gravitational drop of the entire installation. The summary of this technology looks almost identical like a non-steerable device.
SUMMARY OF THE STEERABLE HYDRAULIC JACKING MACHINES:
- Limited steering options to avoid hard obstacles.
- Low accuracy limiting this technology to making installations on short distances and not requiring precision.
- It is not recommended for any gravity installations requiring a imposed drop.
- No possibility of fully trenchless installation between the existing sewage chambers.
- Limited jacking length and installed pipe diameter.
Auger drill rigs
The technology with the use of auger drills is widely used in the construction of sewage installations, including gravity, i.e. requiring a precise slope. Such drilling rigs are very often equipped with a precise teleoptic system for locating the head, which, together with the effectiveness of drilling the head even through hard fractions in the ground, allows for exceptional drilling precision and thus a decrease in the installation performed.
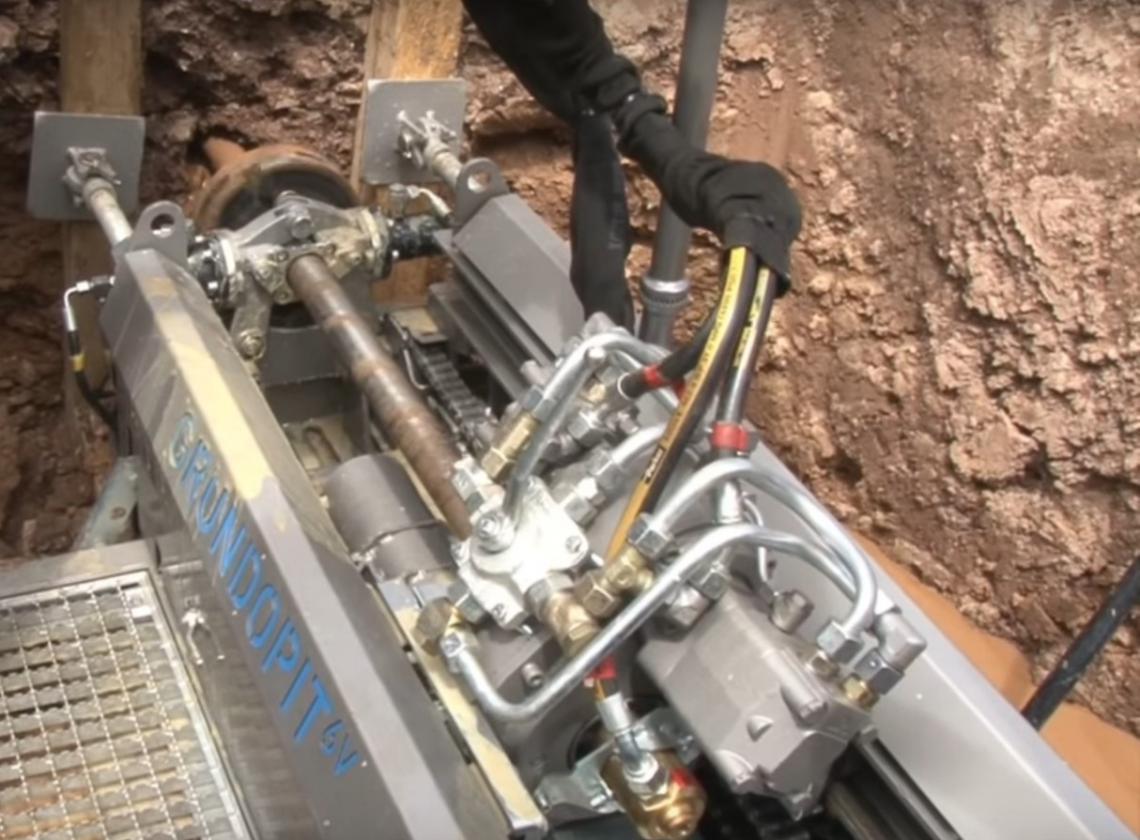
Unfortunately, a drawback of this technology is the need to make a large-sized starting chamber from which the drilling will be carried out. The starting chamber must be up to three meters long (and longer), depending on the size of the machine. The size of the machine, in turn, affects the length of the drill hole / installation and the diameter of the pipes to be installed. Such machines are therefore suitable for the construction of sewage installations, including gravity installations with a precise slope, in undeveloped places or with small buildings, where a large starting chamber for the machine can be made. In the case of works in dense urban buildings, where we are dealing with the construction of an installation between two sewage wells, or when we connect to an existing installation from a spatially limited space, the use of auger drilling rigs requires partial disassembly of the existing infrastructure, demolition of sewage wells, construction of excavations. Some auger drills require the foundation of large DN 2000 wells for operation. Most of the wells in dense urban agglomerations are usually DN 1200, sometimes DN 1000 and DN 1500. Therefore, it is not possible to make a fully trenchless installation with such a auger drilling machine. It is often necessary to make installations between the existing DN 1200 chambers, without the possibility of their disassembly or when their disassembly would entail significant communication difficulties in the vicinity of the works being carried out. There are smaller auger drills available on the market, which enable to work from a sewage well, e.g. DN 1200. Unfortunately, these devices have a very limited range of pipe diameters and installation lengths that we can implement with their use. Typically 15-20 meters of installation length for a pipe with a maximum diameter of 273 mm.
SUMMARY OF THE AUGER DRILLING RIG:
- Limited application possibilities due to large dimensions of the machines.
- The high accuracy and high efficiency overcoming obstacles.
- No possibility of fully trenchless installation between existing sewage chambers.
Horizontal drilling rigs (HDD technology)
It is widely accepted that it is the most advanced technology among all for trenchless construction of underground installations. This is true in some aspects. This technology is the only one that allows the construction of installations with lengths of up to hundreds of meters. It can be used to make installations under river and canal beds, or under very wide communication routes, multi-lane roads with accompanying tracks and pavements. The technology is equipped with a drilling route location system and the possibility of full horizontal and vertical control. Therefore, it can be used to make installations in densely built-up areas with other underground installations, obviously having the design of the existing underground network. All installations can be made with the required precision. It is possible to perform gravity sewage.
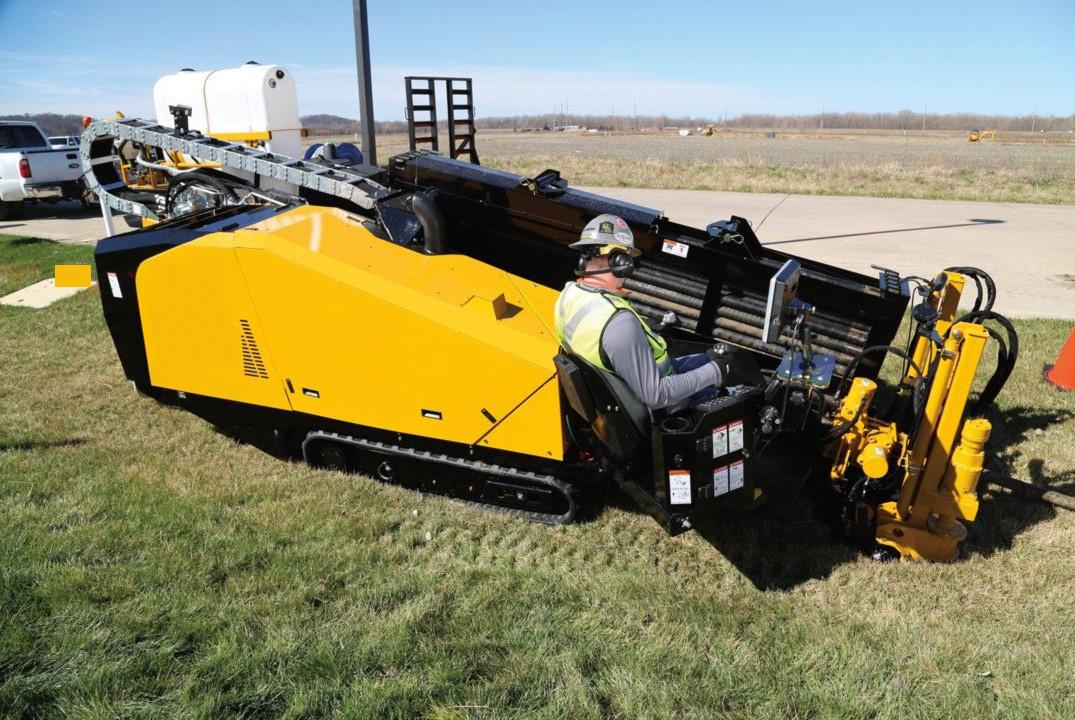
A significant disadvantage of the horizontal drilling technology is unfortunately, the large amount of space required for the installation of the drilling rigs. Even the smallest horizontal drilling rigs require several square meters of area for their preparation to work. In many cases in dense urban buildings, unfortunately we do not have such space. Another reason for limiting the use of drilling rigs is the large bend radius for the rod assembly. To obtain a straight section of the installation with a given slope, it is necessary to start drilling in the ground a few meters before the actual start of the planned installation to ultimately obtain a straight section between the start and end point of the installation to be constructed. Most often, in such cases, it is not possible to do without a partially excavated construction. This rules out the complete trenchlessness of this technology. Building an installation between the existing wells is not feasible with this technology. This technology also makes it impossible to perform installations with a precise slope in difficult ground conditions. The head during drilling, when it encounters hard obstacles, will have a problem with overcoming them without losing the set direction.
SUMMARY OF THE HORIZONTAL DRILLING TECHNOLOGY:
- High accuracy and high efficiency of the installation.
- The possibility of making installations with lengths of hundreds of meters.
- Limited application possibilities due to large dimensions of the machines.
- No possibility of fully trenchless installation between the existing sewage chambers.
- Problem with overcoming hard obstacles.
Gravity drilling rig
So how and with what technology can you build underground installations with a length of 50 meters and more, performing the functions of gravity channels, i.e. requiring high precision of slope? How to make an underground pipe in a densely built-up urban infrastructure with a very limited construction site? How to avoid the necessity to shut down traffic routes, adjacent and / or coexisting in the place of work, during the works? The elements of new installations, already existing in the form of sewage wells, very often are located in the center of a busy street or sidewalk. How to implement a new installation non-invasive to the environment? How to install in places with hard underground obstacles? How to make an underground installation from well to well fully trenchless? In response to these needs, our technology of Gravity Drilling was created.
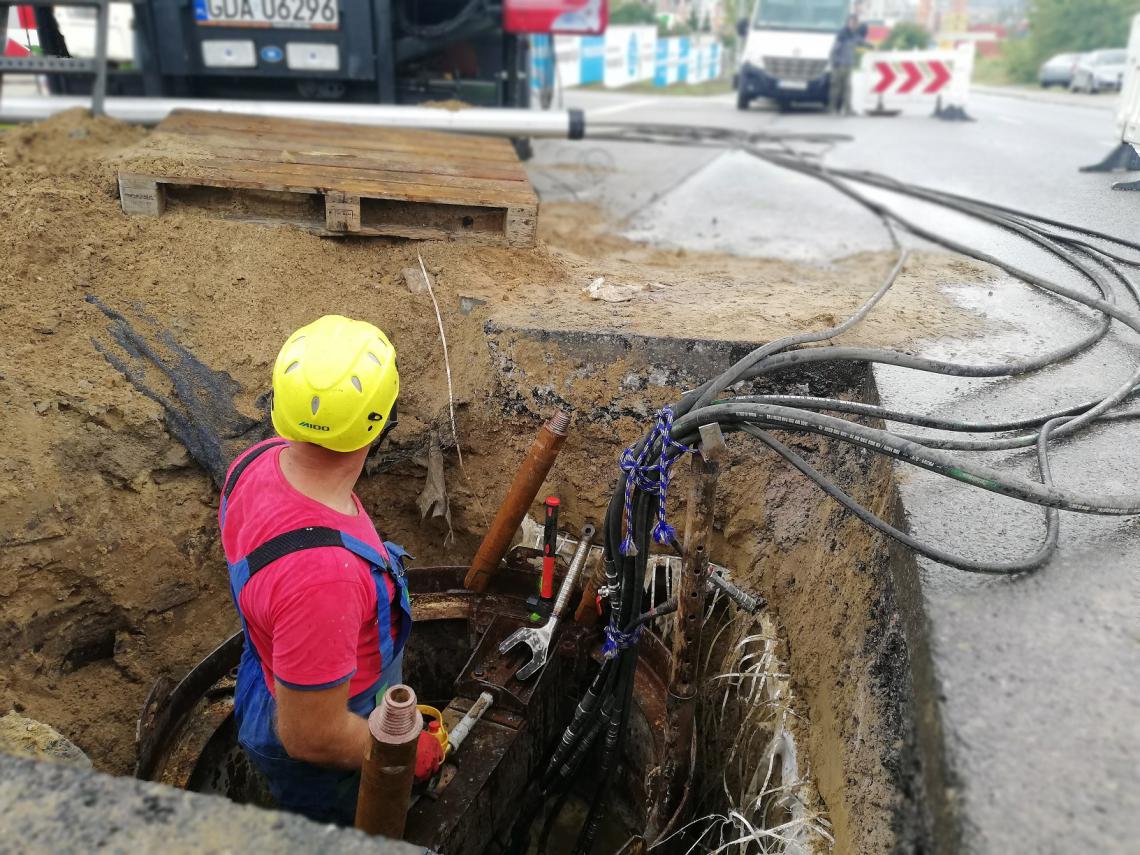
As a company that has been dealing with the construction of underground installations using trenchless methods for over twenty years, we have faced a whole lot of unusual challenges. Not all of them could be implemented fully properly, with the use of generally available machines and technologies. Years of experience have resulted in the development of our own, innovative and very effective technology, designed for the most precise gravity installations. We have developed our own device solution that allows for fully trenchless, non-invasive in the existing infrastructure, precise, effective and cheap construction of all types of underground sewage systems. In particular, our technology is unrivaled in the construction of new installations between the existing, typical DN1200 sewer manholes. We make such installations 100% trenchless, without the need to disassemble and exclude any part of the existing infrastructure, such as road, pavement, and track from use. Our drilling rig, as the only one in the category of machines for trenchless installations, allows installation in an existing DN 1200 well. It has the ability to overcome even the toughest obstacles without losing the given direction, and allows for installations with a length of 50 meters or more (typical distance between wells), using pipes with diameters up to 500mm.
Significant advantages / features of our technology:
- the starting chamber is a well (new or existing) DN 1000, DN 1200 or larger
- the possibility of implementing installations from typical wells without the need to interfere with the surrounding infrastructure
- the drilling machine is placed in the well through a typical DN 600 manhole
- the installation does not require any excavation, work begins and ends in the wells
- no need for starting chambers and their drainage
- the possibility of mounting the machine in wells of any non-standard shape and possible work from the excavation using a mobile starting chamber or adapters
- the ability to perform work from a starting well with low mechanical strength
- the possibility of working in a well equipped with space limiting elements without the need to disassemble them
- it is possible to drill at any depth
- the technology allows to make the sewer with an accuracy of 2 ‰, depending on the soil conditions
- the drill spindle can work at the very bottom and under the cover of the well
- drilling is possible below the groundwater level, and this applies to the entire bore path, including the area around the well
- work in soils with drilling classes: II, III, IV, V: sand, gravel, clay and soft rocks, medium: marly limestones, order clay, marls, sand shales, rubble, concrete obstacles
- the technology used does not reduce soil compaction, but allows the zone around the pipe to be laid to be compacted, which has a positive effect on the stability of the installation
- during drilling works on active collectors, there is no need to block sewage
- the highest efficiency of the installation compared to other available technologies
The main advantage of the technology with the use of the Gravitational Drilling Rig is the possibility of making the installation from the existing sewage well, without any interference with the existing infrastructure.
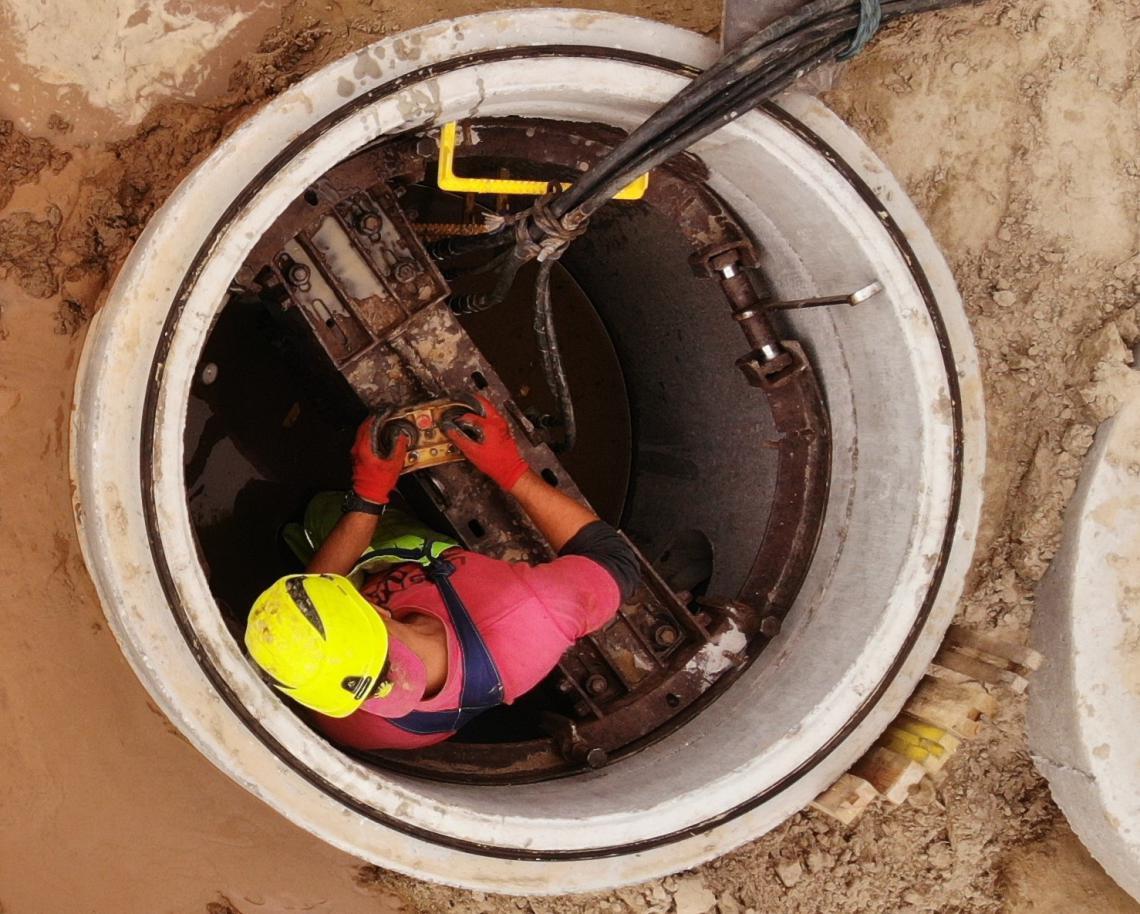