As part of the construction by the Investor - the Robyg company, of a complex of residential buildings "Zajezdnia Wrzeszcz", located at Bolesława Chrobrego Street in Gdańsk, the MIDO company built a rainwater drainage system. The length of the installation was 15 meters, with a design slope of 2%. PP Modular Pipes with a diameter of 225 mm were used.
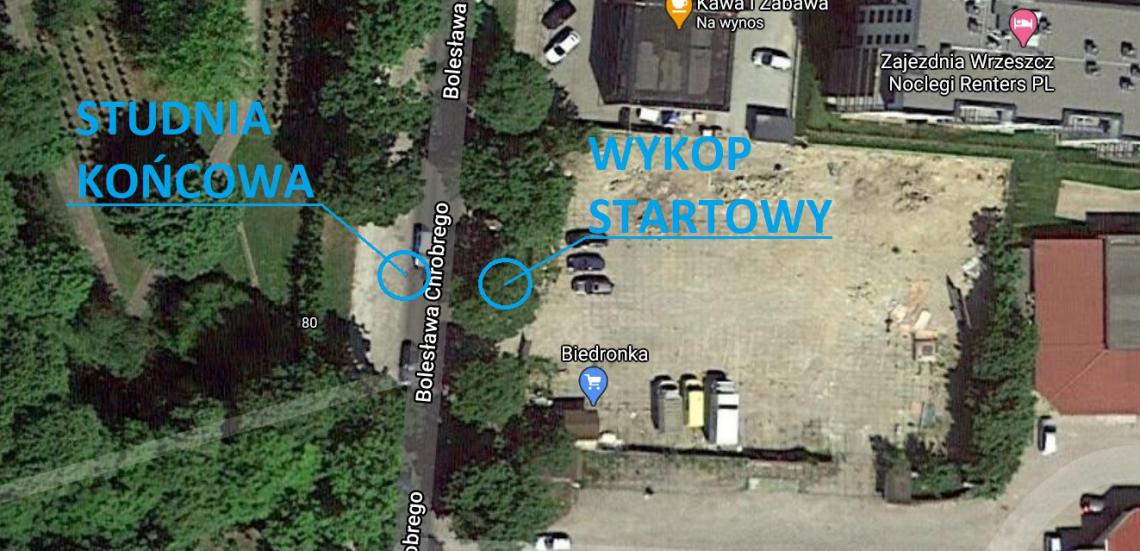
The course of the installation covered the area between the existing sewerage well, located in Bolesława Chrobrego Street, and the starting chamber, located on the construction site of a residential complex.
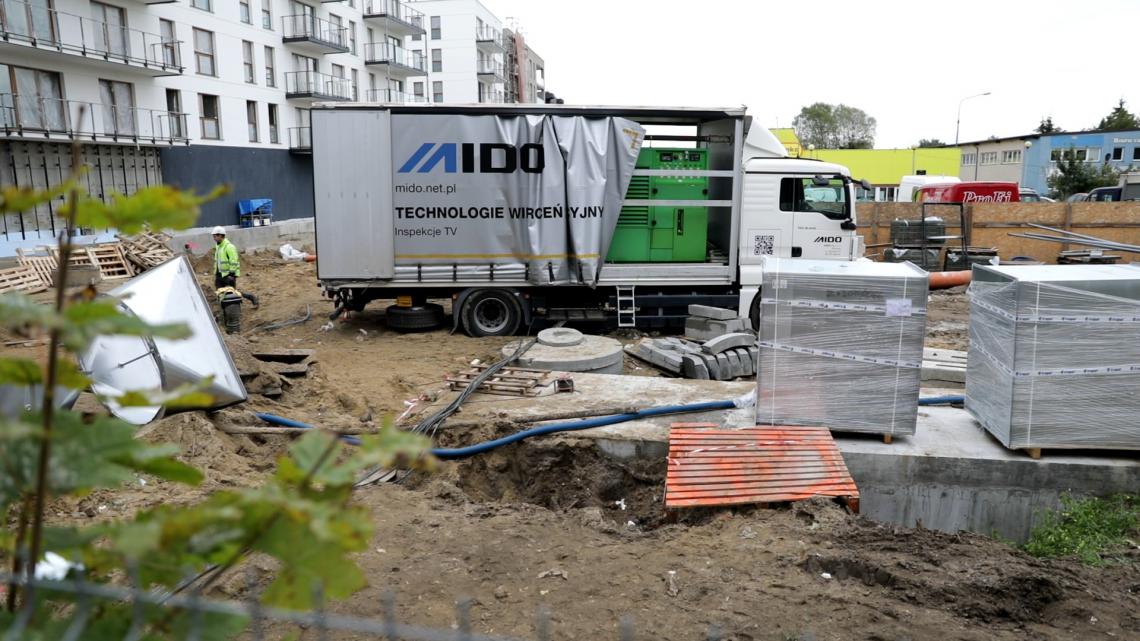
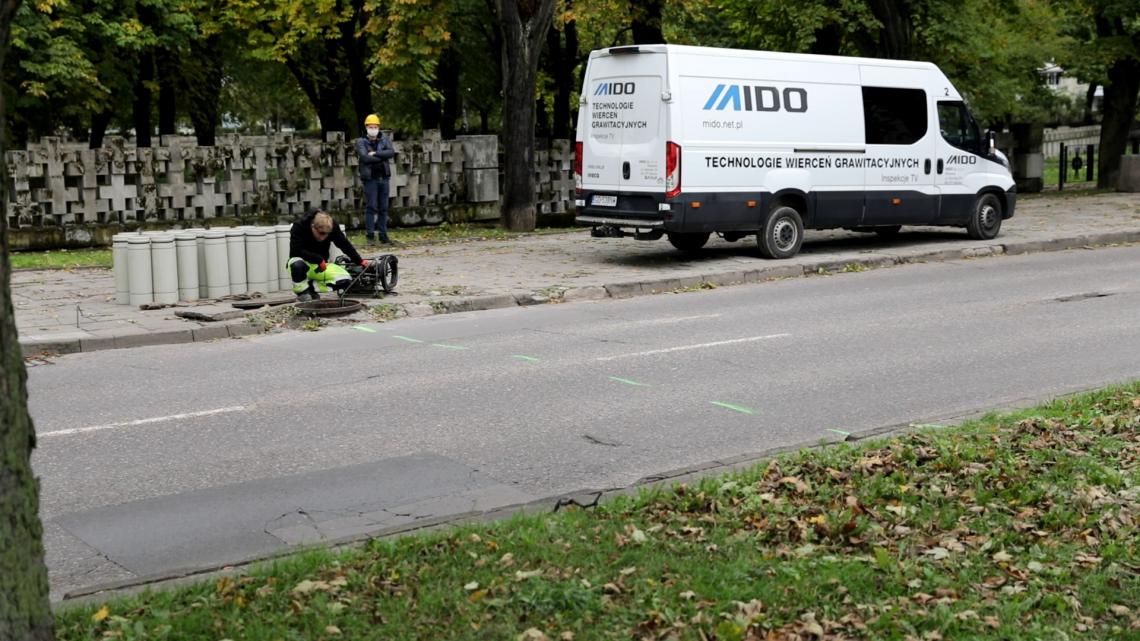
Originally, the installation was to be made using other trenchless technologies, including the installation of a steel casing pipe with a jacking machine, the so-called mole, due to lower costs. However, potential contractors withdrew their offers, mainly due to insufficient space for the starting chamber. The second important reason was the need to perform the installation with very high precision, resulting from the vicinity of the underground water supply system running in the construction area. The sewage system under construction was to run a dozen or so centimeters away from the water supply system. Damaging it would cause serious problems and additional significant costs.
In the first stage of the installation, a drilling was made from the starting chamber, in which a sewage well DN 1200 was first built, and then a Gravity Drilling Rig was installed.
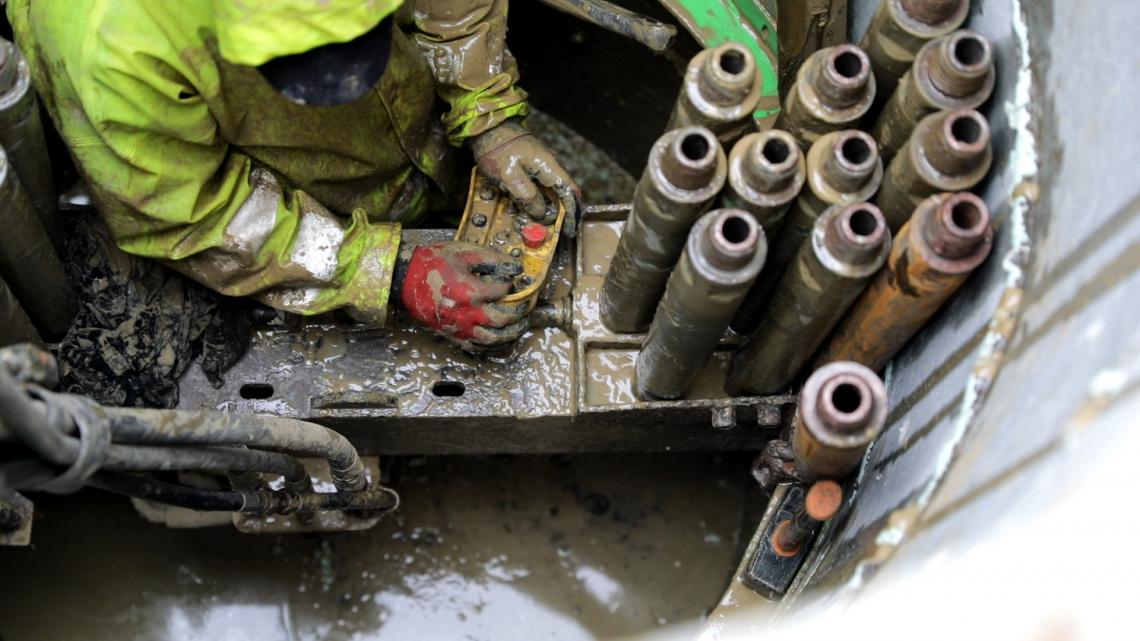
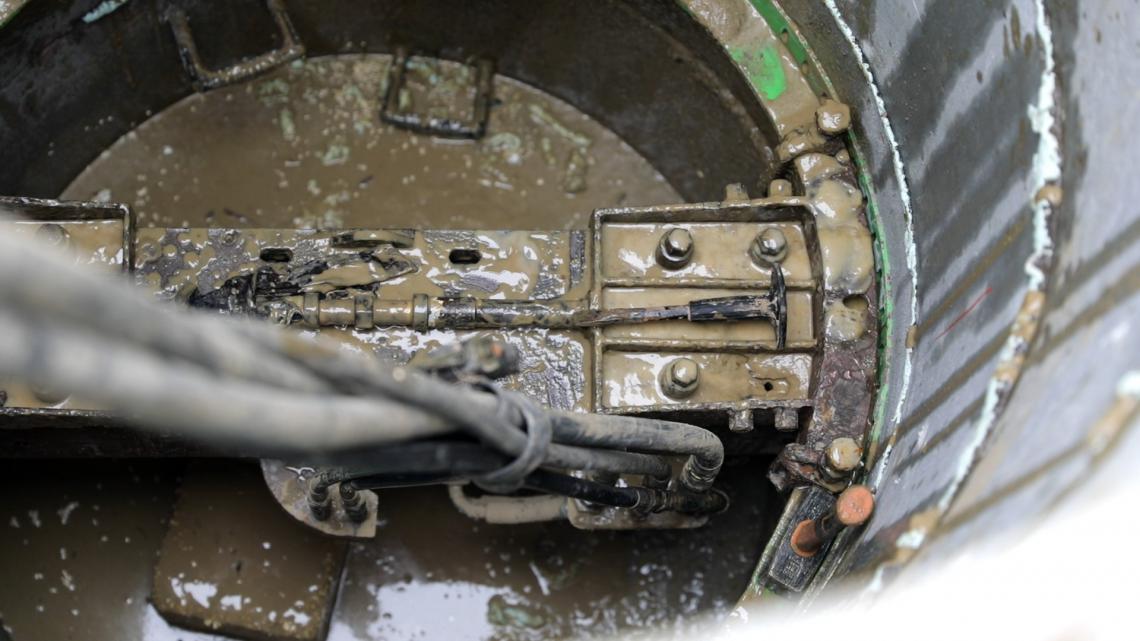
After reaching the final well, with the retooled machine, the pulling of the pipe, built of successive segments of Modular Pipes, was started. Previously, of course, it was necessary to drill a hole made with a pilot drill, using a core drill adapted to the diameter of the pipe to be installed. In this case, this activity was abandoned due to practical tests of the new solution of reaming heads. Most of the typical sewage chambers can be easily drilled with just such a head. The problem can only occur in wells with low mechanical strength, where the use of a reamer instead of a core drill may damage the well components. One of the advantages of the Gravity Drilling Rig technology is overcoming hard obstacles, including well construction elements, not by using the force of pushing or pulling the machine, but by properly selecting the geometry of the drill head and the ability of the machine to fully and smoothly control all operating parameters during drilling.

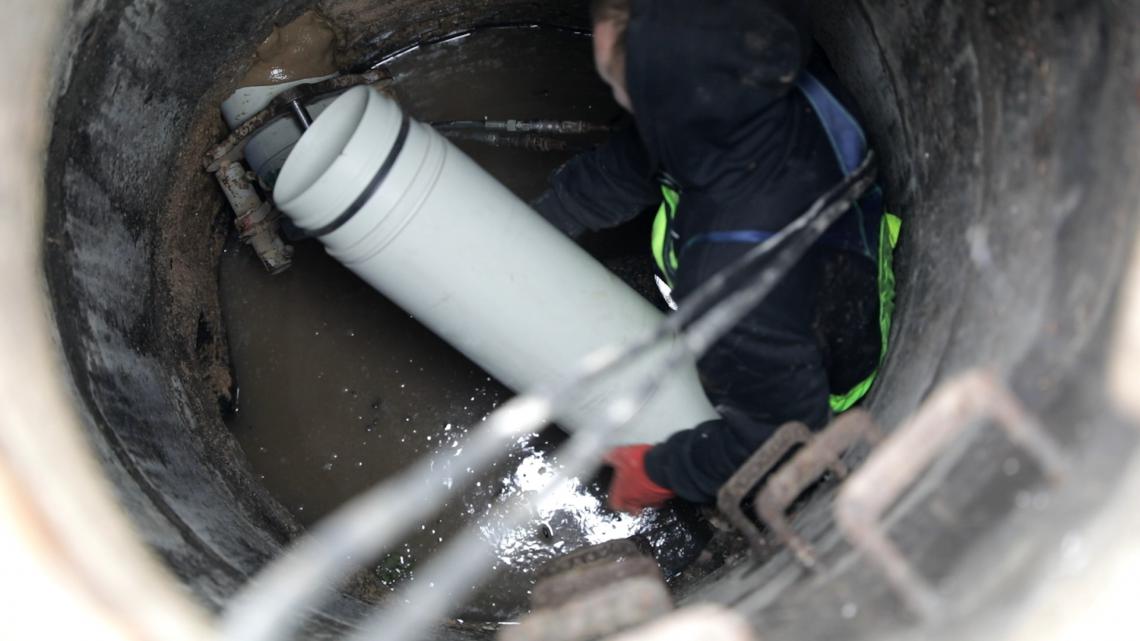
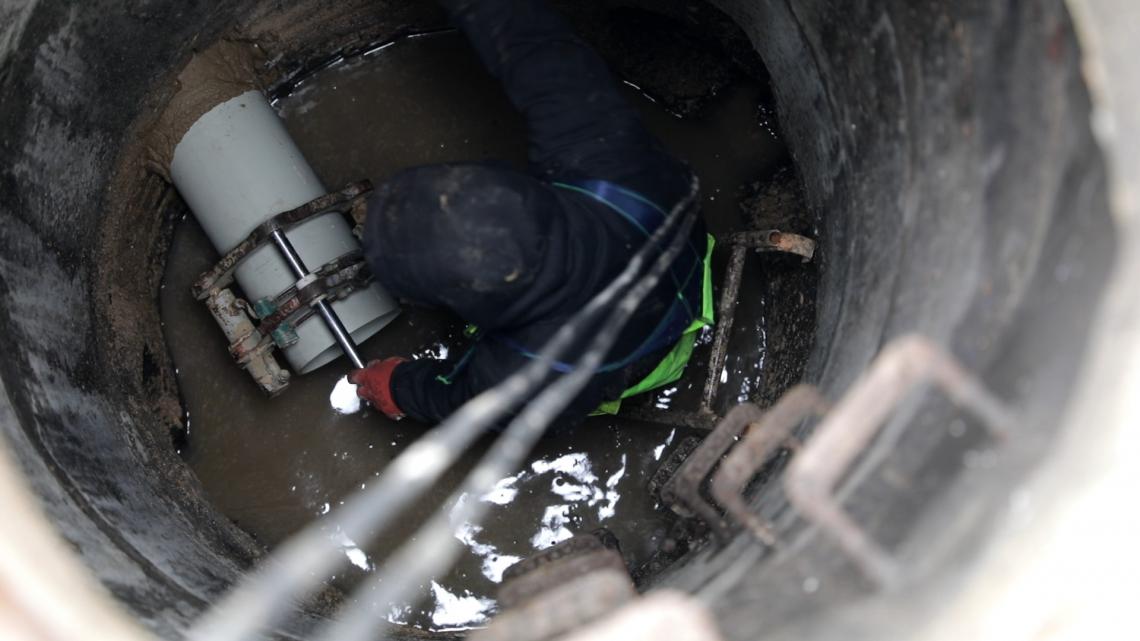
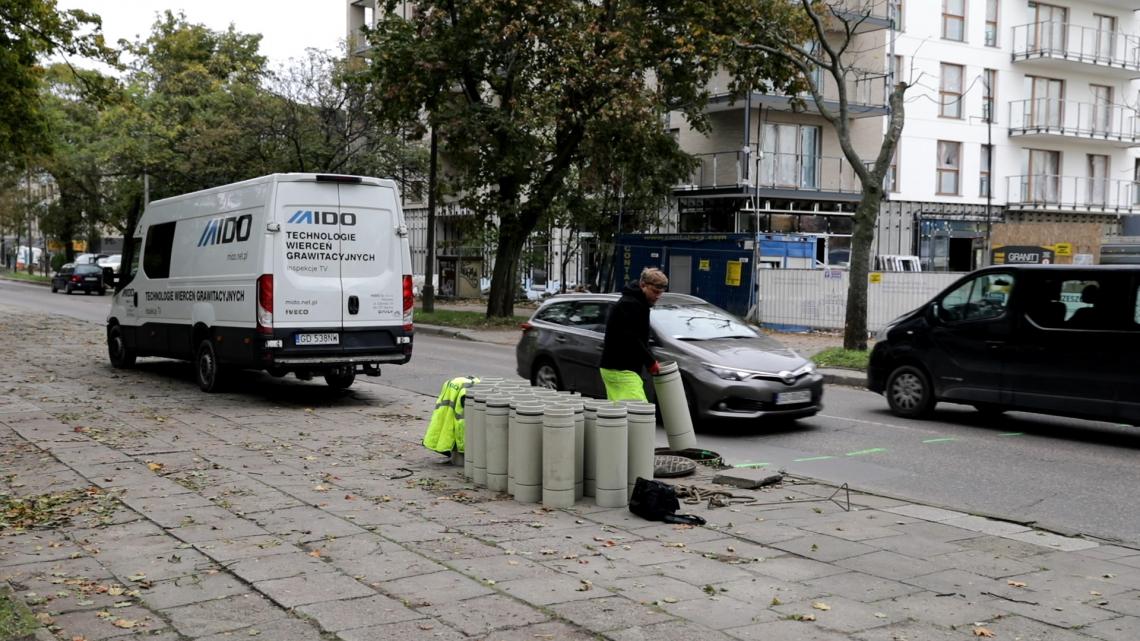
One of the advantages of the Gravity Drilling technology is the ability to work only within the sewage wells involved in the installation. The Modular Pipes we use allow them to be joined in a place limited by the well. The connection itself is effective, tight and durable. We connect the individual pipe segments using a hydraulic squeezer that presses one end of the pipe into the other.
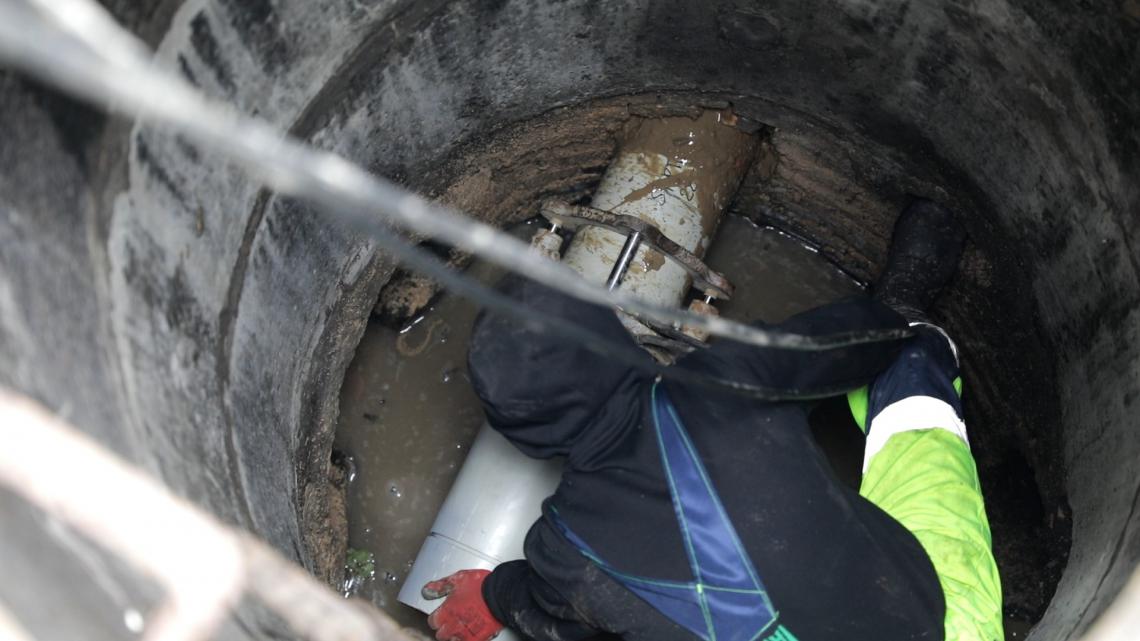
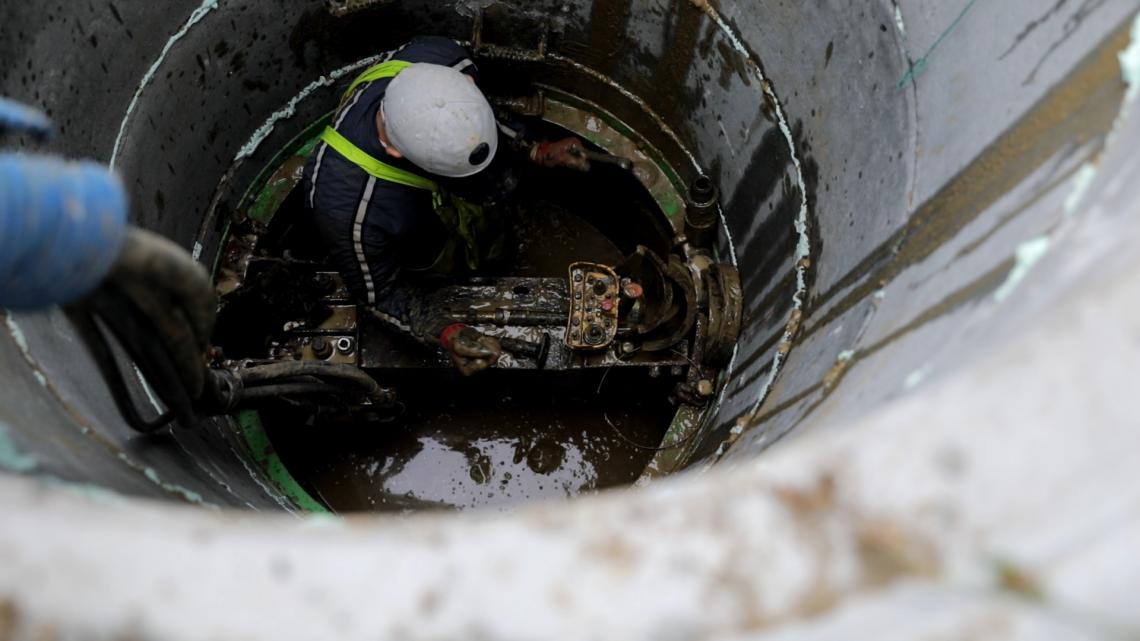
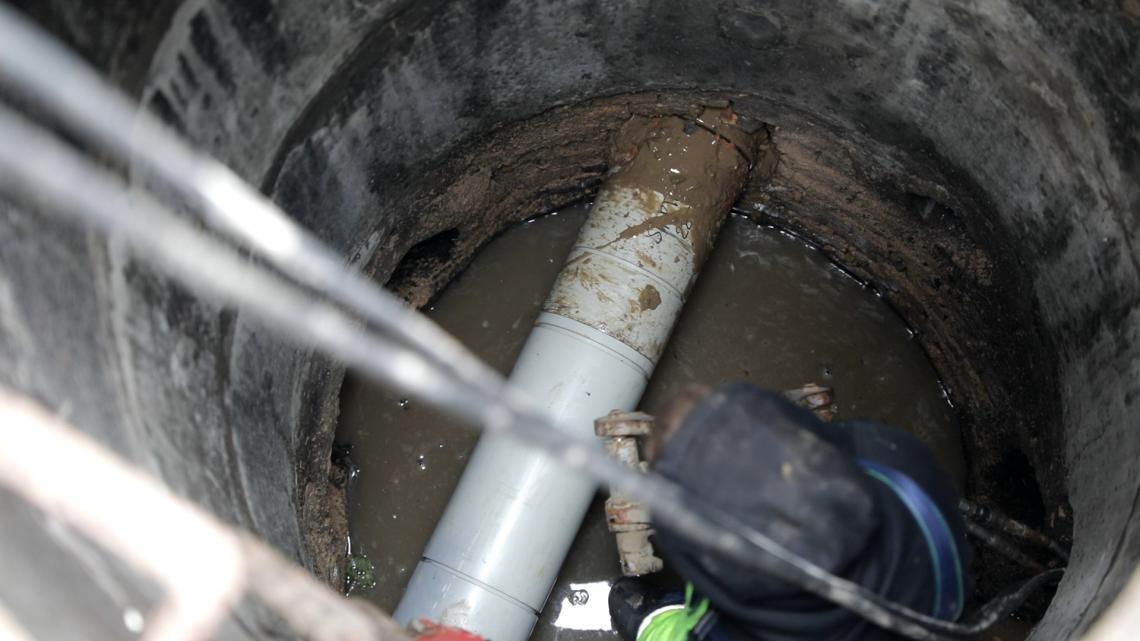
Finally, just before reaching the starting well, a reaming of the well wall is made to allow the installation of the pipe to be introduced into the starting well.
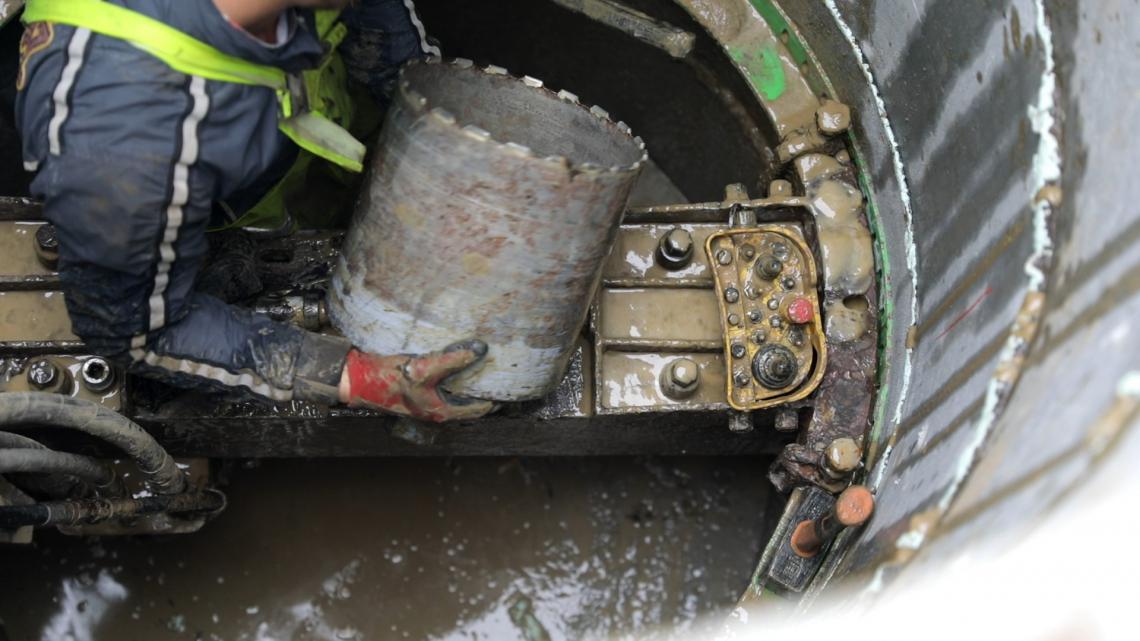
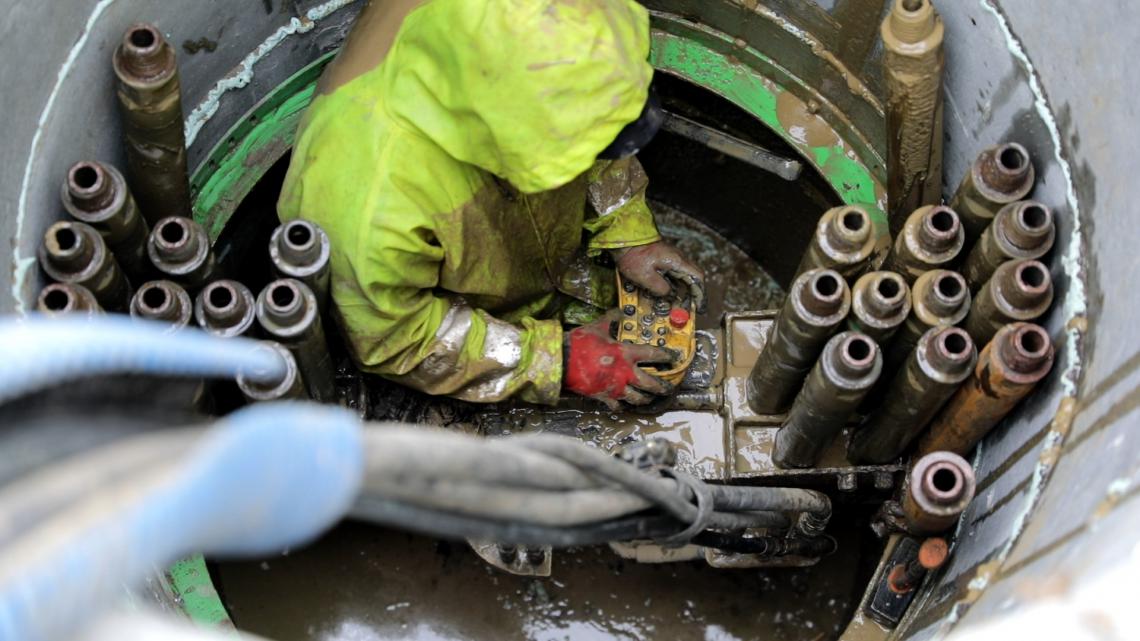
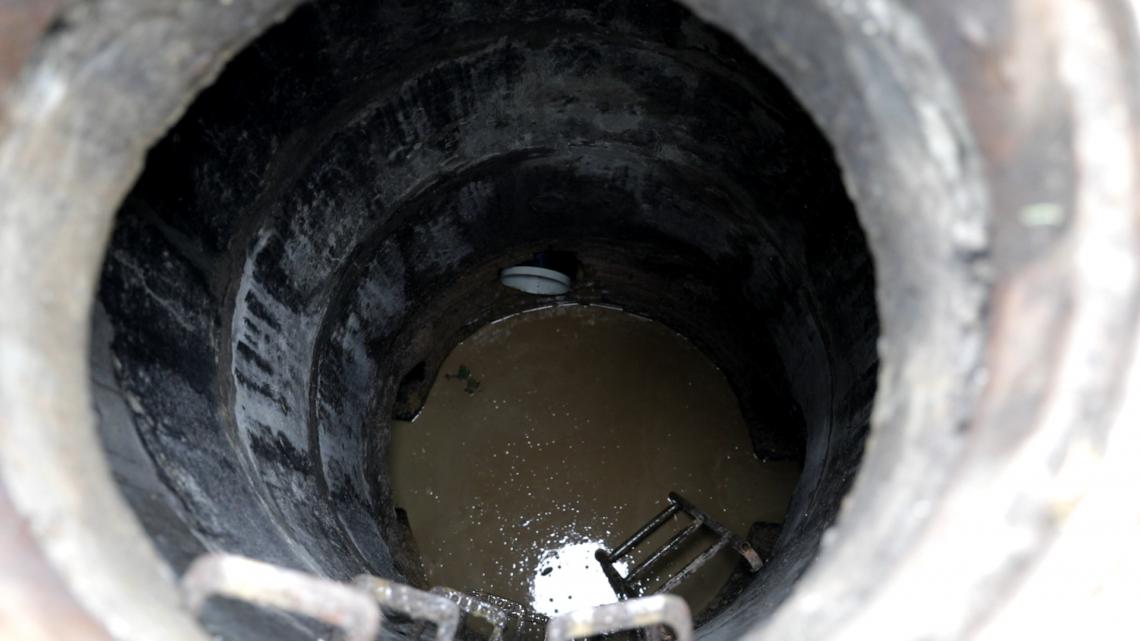