Renowacja kanalizacji deszczowej w Gdańsku przy ulicy Podwale Grodzkie, w ramach projektu "Renowacja odcinków kanalizacji deszczowej w ulicach Powstańców Warszawskich, Podwale Grodzkie oraz Grunwaldzkiej w Gdańsku".
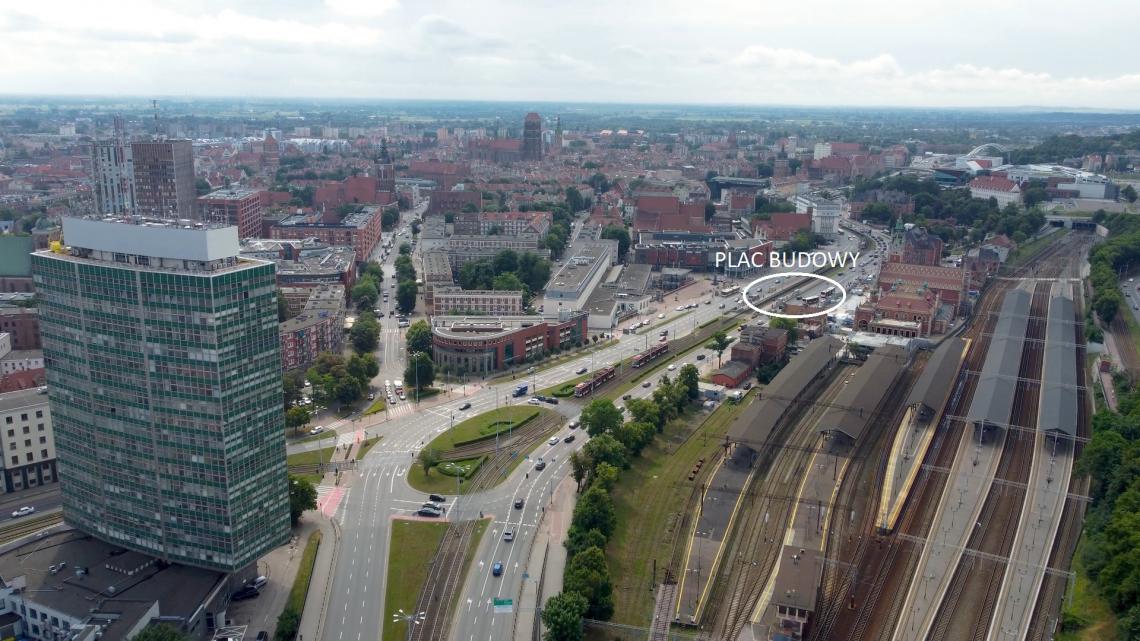
Zakres prac obejmował:
- przygotowanie i uzgodnienie tymczasowej organizacji ruchu i uzyskanie zgody zarządcy drogi na zajecie pasa (uwaga: studnia w torowisku),
- zabezpieczenie miejsca wykonywania prac (kanału oraz przyłączy bocznych), poprzez zapewnienie kontrolowanego odprowadzenia wody deszczowej w okresie wyłączenia z użytkowania odcinka KD tak, aby podczas realizacji prac nie doszło do podtopień
- inspekcję telewizyjna przedwykonawcza
- czyszczenie rurociągu
- wykonanie pomiarów przed rozpoczęciem prac,
- zainiektowanie całego odcinka kanału z wypełnieniem wszystkich wolnych przestrzeni
- wykonanie przewiertu i montażu nowej rury po śladzie dawnego kanału
- inspekcja telewizyjna powykonawcza
- uporządkowanie miejsca prowadzenia prac
- sporządzenie dokumentacji powykonawczej
Projekt polegał na bezwykopowym ułożeniu kanału z rur modułowych PP 400x22.7 w miejsce uszkodzonego kanału przebiegającego pomiędzy istniejącymi studniami kanalizacyjnymi. Prace należało wykonać z wykorzystaniem istniejących studni i bez wykonywania wykopu otwartego i naruszania nawierzchni. Renowację należało wykonać po istniejącej trasie.
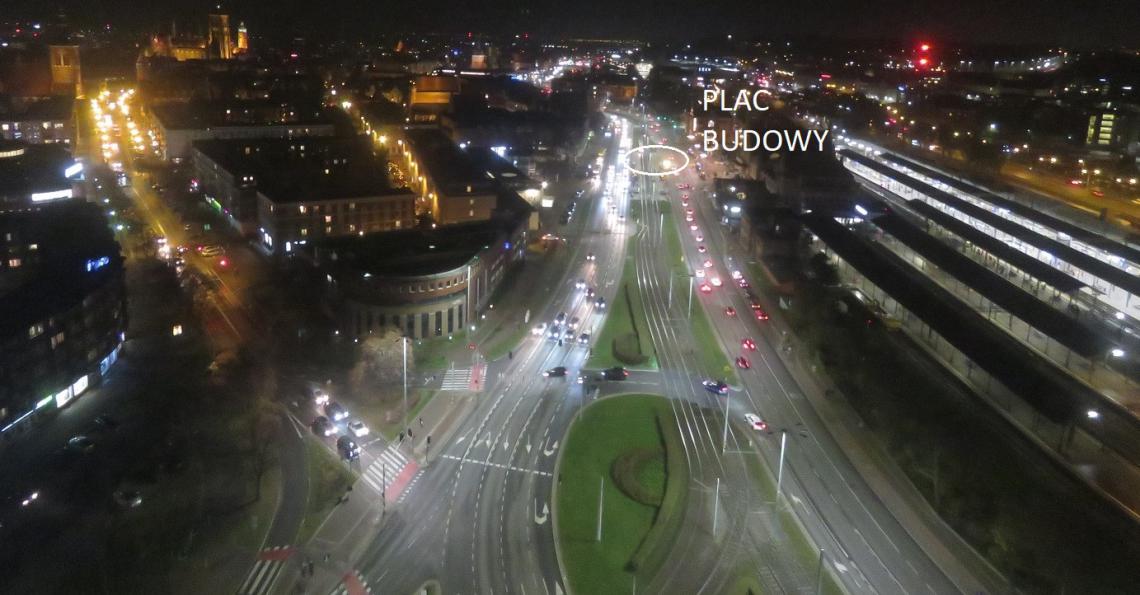
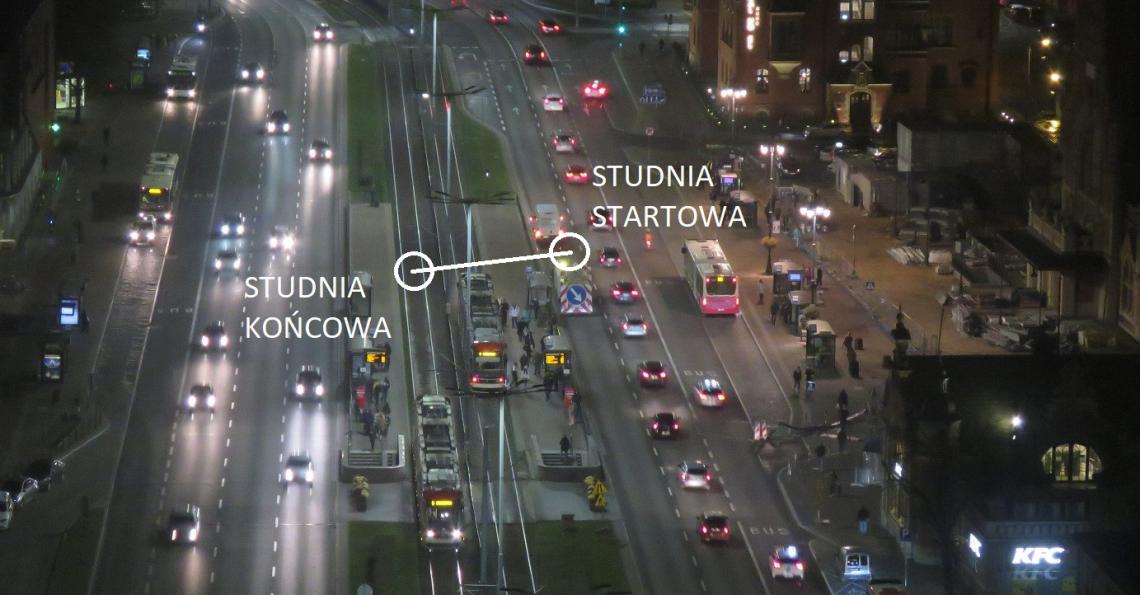
Trudność w realizacji tego zadania wynikała z dwóch istotnych spraw:
Uszkodzony kanał był CAŁKOWICIE niedrożny. Całość projektu obejmowała wykonanie renowacji czterech odcinków kanału pomiędzy istniejącymi studniami kanalizacyjnymi. Trzy z nich udało się zrealizować naszemu zleceniodawcy przy pomocy innej technologii renowacyjnej. Niestety ostatni odcinek, położony przy ulicy Podwale Grodzkie był niedrożny i uszkodzony do tego stopnia, że niemożliwe było wykonanie inspekcji systemem z kamerą inspekcyjną. Zły stan techniczny wykluczał technololgię renowacji przy pomocy wykładziny rękawowej z włókna szklanego.

Po niespełna trzech metrach i napotkaniu na wyjątkowe przeszkody w postaci załamań istniejącego kanału, inspekcję trzeba było przerwać. W przeciwnym razie groziła nam utrata cennego sprzętu do inspekcji CCTV.
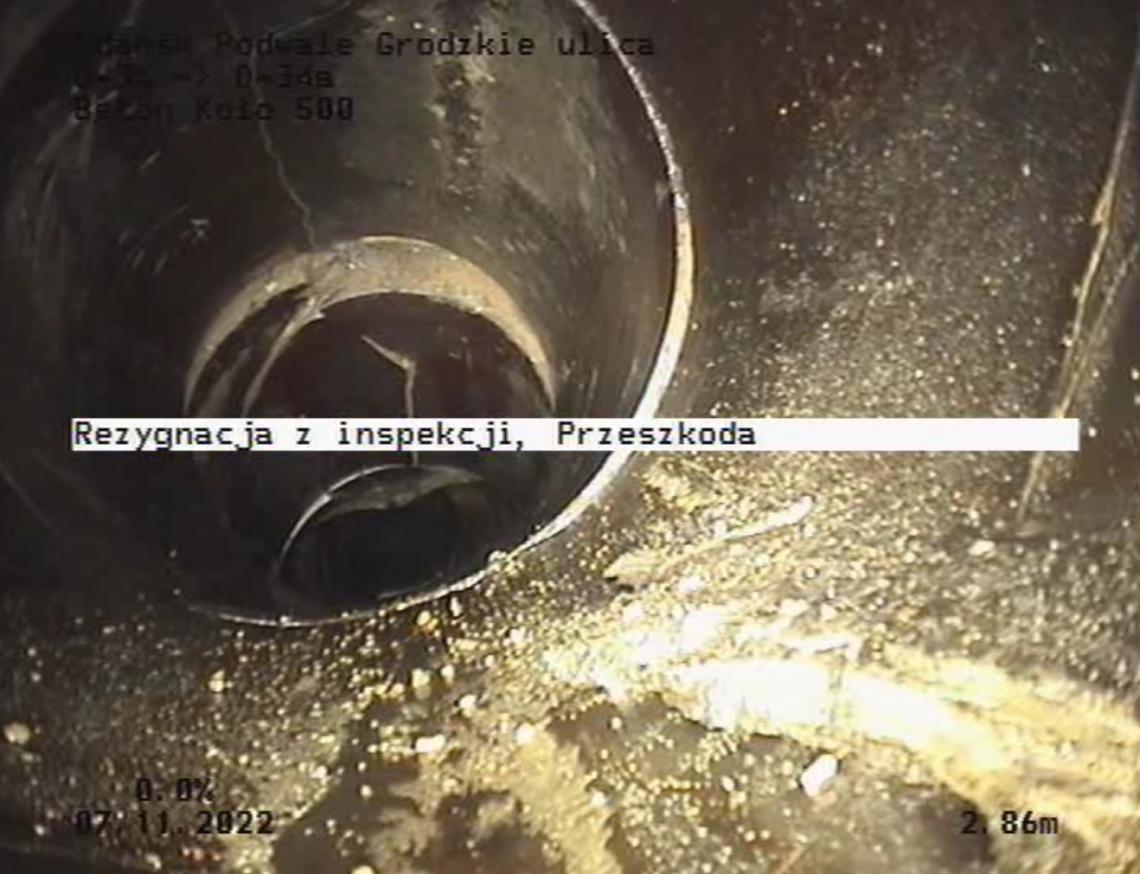
Ponadto zamawiający z oczywistych nam powodów nie dopuszczał metody renowacji w postaci Krakingu. Przede wszystkim uszkodzony rurociąg przed jego odbudową, trzeba było wzmocnić wypełniając go zaczynem iniekcyjnym. Przy tak mocno uszkodzonym istniejącym przewodzie kanalizacyjnym, brak tej operacji, przy dodatkowym odziaływaniu wibracjami podczas renowacji metodą Krakingu, gwarantował katastrofę budowlaną i jej konsekwencje w postaci strat liczonych w milionach złotych. Inspekcja przedwykonawcza wskazała nam, że skoro istniejący kanał jest tak uszkodzony, to oznacza że grunt wokół niego jest bardzo niestabilny, obfity w liczne puste przestrzenie i luźne frakcje. Wykonanie renowacji przy pomocy Krakingu lub innej zbliżonej metody bezwykopowej, spowodowałoby nieuniknione tąpnięcie wywołane wibracjami, zarówno samego kanału jak i gruntu wokół niego i nad nim. A na skutek tego zapadnięciu uległaby główna arteria w Gdańsku oraz sąsiadujące z nią torowisko tramwajowe, będące ważnym łącznikiem komunikacji centrum miasta z jego zachodnią częścią. Nasza technologia w przypadku renowacji tak uszkodzonych sieci, obejmuje w pierwszym procesie wypełnienie zaczynem iniekcyjnym właśnie po to, by uzyskać stabilną przestrzeń w miejscu uszkodzonego przewodu. Dopiero w kolejnych etapach podejmowane są działania naprawcze.
Kolejnym istotnym problemem było samo miejsce prac, teren budowy. Ulica Podwale Grodzkie a w szczególności jej część sąsiadująca z Dworcem PKP Gdańsk Główny, to jeden z kluczowych węzłów komunikacyjnych.
Studnia startowa znajdowała się na skrajnym lewym pasie trzypasmowej ulicy Podwale Grodzkie.
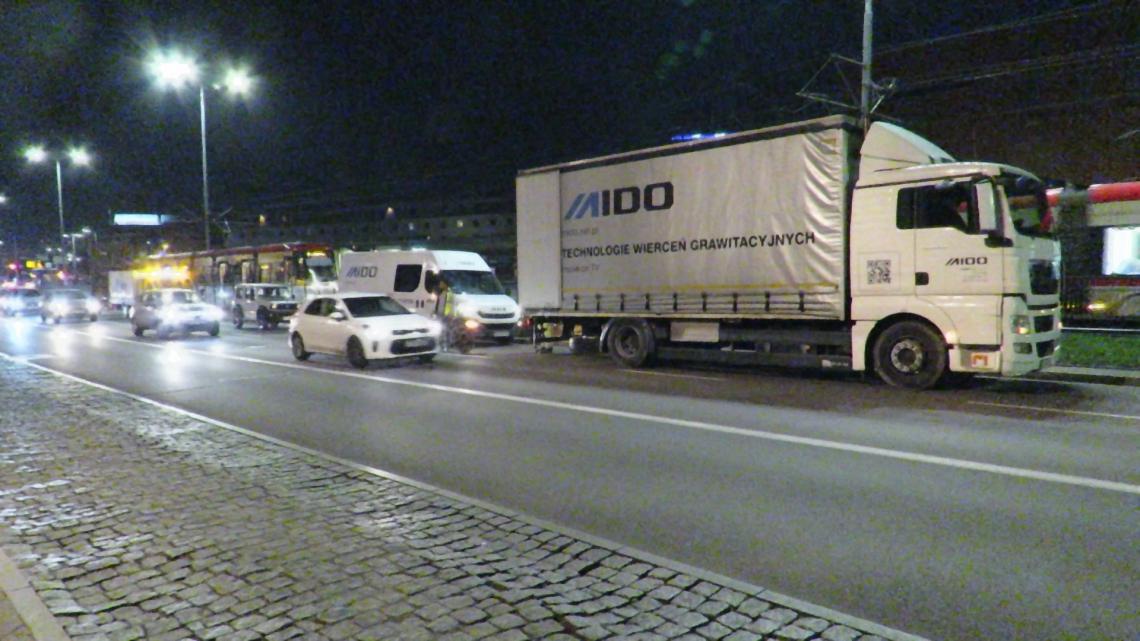
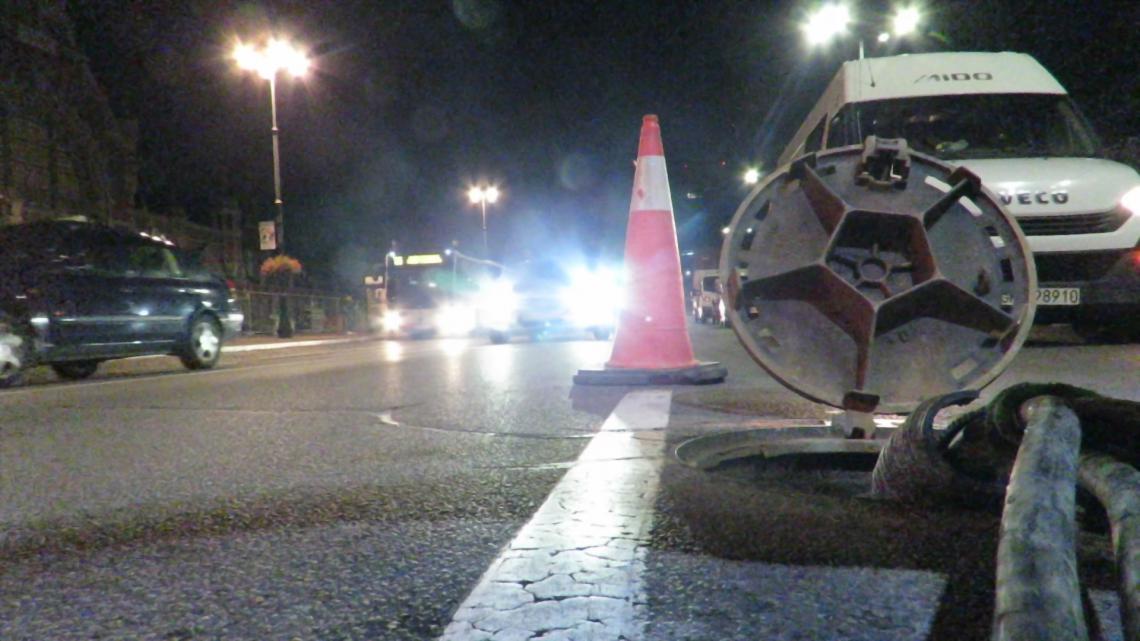
Studnia końcowa zlokalizowana była pomiędzy torowiskiem tramwajowym.
Instalacja wymagająca odbudowy przebiegała pod trzypasmową ulicą oraz pod torowiskiem tramwajowym. O jakimkolwiek zamknięciu tego węzła na czas prowadzenia prac, absolutnie nie mogło być mowy. Zastosowanie jakiejkolwiek innej technologii, wiązałoby się w z wyłączeniem z ruchu znacznej części ciągów komunikacyjnych lub nawet ich całościowego zamknięcia na kilka dni roboczych. To spowodowałoby totalny paraliż komunikacyjny w centrum Gdańska. Ponadto jakikolwiek błąd w realizacji, skutkowałby uszkodzeniem nośności gruntu wokół budowy, wskutek czego nawierzchnia drogowa oraz torowiska uległyby zniszczeniu.
Z tych powyższych powodów, jedyną technologią umożliwiającą wykonanie robót w pełni bezwykopowo oraz bezpiecznie dla otaczającej infrastruktury, okazała się nasza technologia Wiercenia Grawitacyjnego.
Prace renowacyjne podzieliliśmy na trzy kluczowe etapy.
ETAP 1. Przygotowanie uszkodzonego odcinka sieci do renowacji.
Odbudowę sieci rozpoczęliśmy od wypełnienia zaczynem iniekcyjnym uszkodzonego przewodu kanalizacyjnego. Zastosowaliśmy do tego mieszankę wypełniającą GRUNTON DR-1.5.
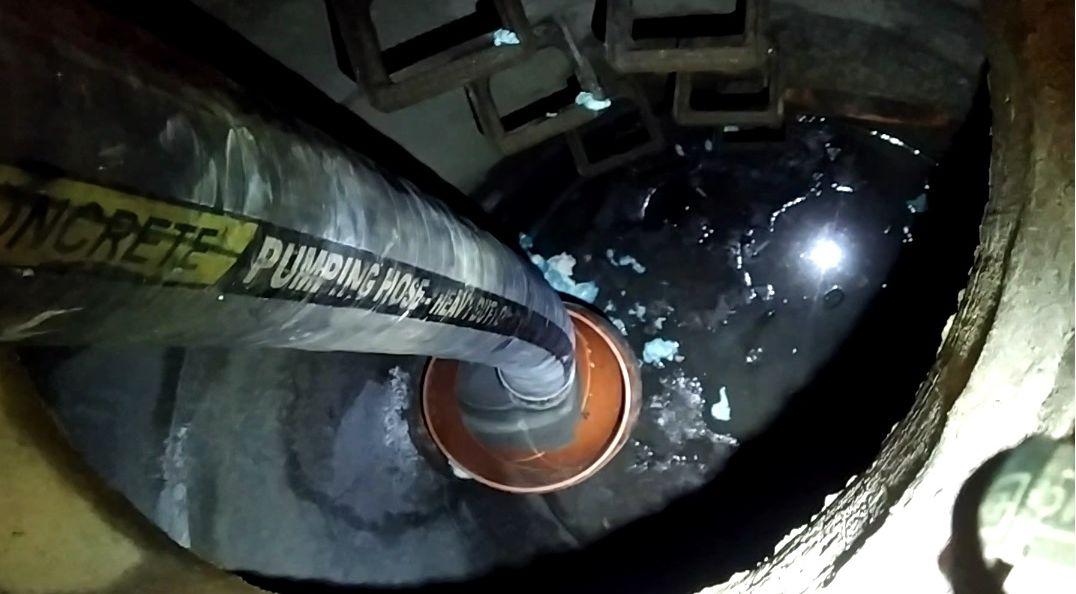
Aby proces wypełniania przebiegł optymalnie, przed samym wypełnianiem z obu stron uszkodzonego przewodu kanalizacyjnego zostały zamontowane kolanka dopływowe dla mieszanki wypełniającej.
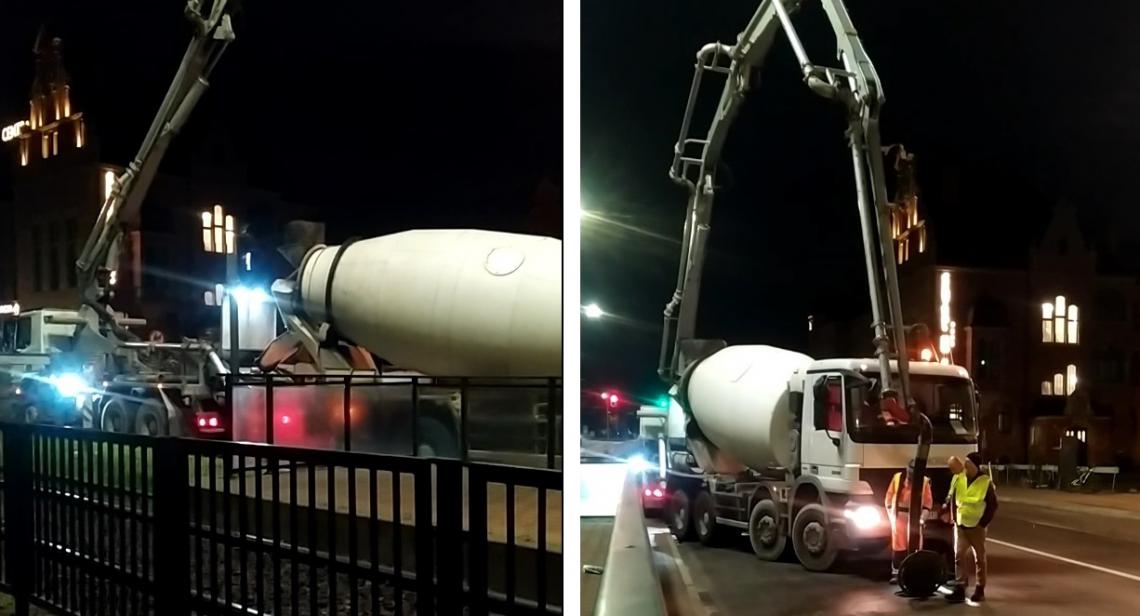
Na tym zakończyliśmy pierwszy dzień prowadzenia budowy. Zaczyn iniekcyjny musi stężeć i utwardzić się na tyle, by możliwe było przystąpienie do kolejnego etapu budowy.
Warto dodać, że w podobny sposób, czyli poprzez zastosowanie zaczynu iniekcyjnego, realizujemy budowy nowych odcinków sieci kanalizacji grawitacyjnej, gdy na jego trasie napotykamy na przeszkody typu puste przestrzenie. Pokonanie takiej pustej przestrzeni głowicą wiercącą jest niemożliwe z uwagi na brak możliwości sterowania wiertłem podczas kolejnego etapu, opisanego poniżej.
ETAP 2. Wykonanie przewiertu pilotażowego.
To kluczowy z punktu widzenia powodzenia w realizacji przy pomocy naszej technologii etap. Od prawidłowości i celności jego wykonania zależy uzyskanie zadanego, projektowanego spadku grawitacyjnego dla nowo budowanej lub naprawianej sieci.
Na czas prowadzenia robót, na każdym etapie, wyłączyliśmy z ruchu jedynie jeden skrajny pas ruchu, na którym znajdował się właz do studni kanalizacyjnej
Jeden z naszych kompaktowych pojazdów technicznych posadowiliśmy w bliskim sąsiedztwie studni startowej. Na nim oraz w nim znajdują się wszystkie urządzenia, zarówno zasilające jak i uczestniczące bezpośrednio w wykonaniu pracy. To znacznie ułatwia i skraca czas budowy.
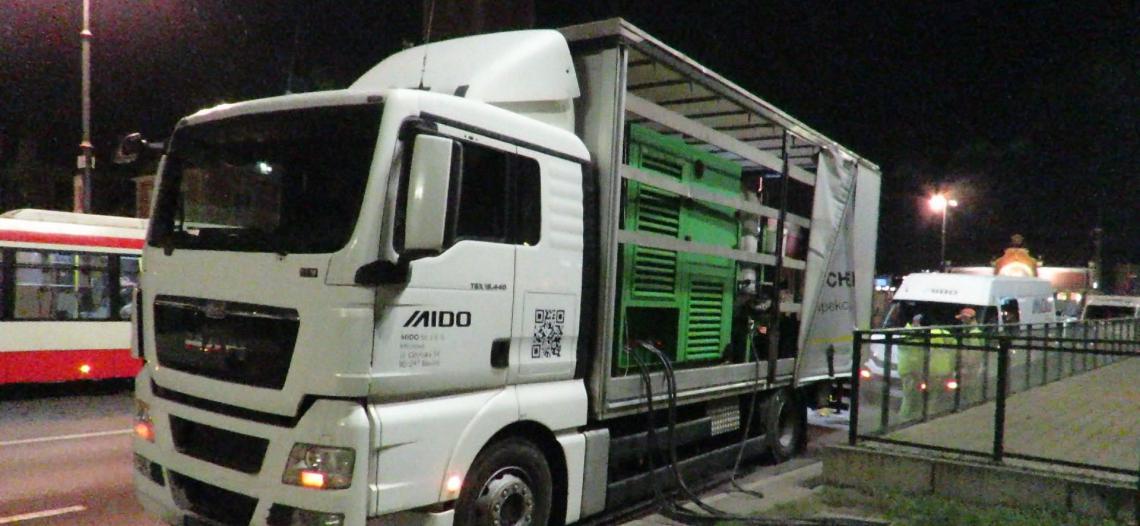
Pry pomocy podnośnika zainstalowanego w pojeździe technicznym zamontowaliśmy maszynę wiertniczą w studni. Tu akurat była to studnia DN 1500. Jak widać na kolejnych zdjęciach, nasza technologia nie wymaga demontażu jakiegokolwiek elementu istniejącej zabudowy terenu, także pokrywy studni. Nasze urządzenia wiertnicze w postaci osobnych elementów wprowadzamy do studni poprzez typowy właz studzienny DN 600.
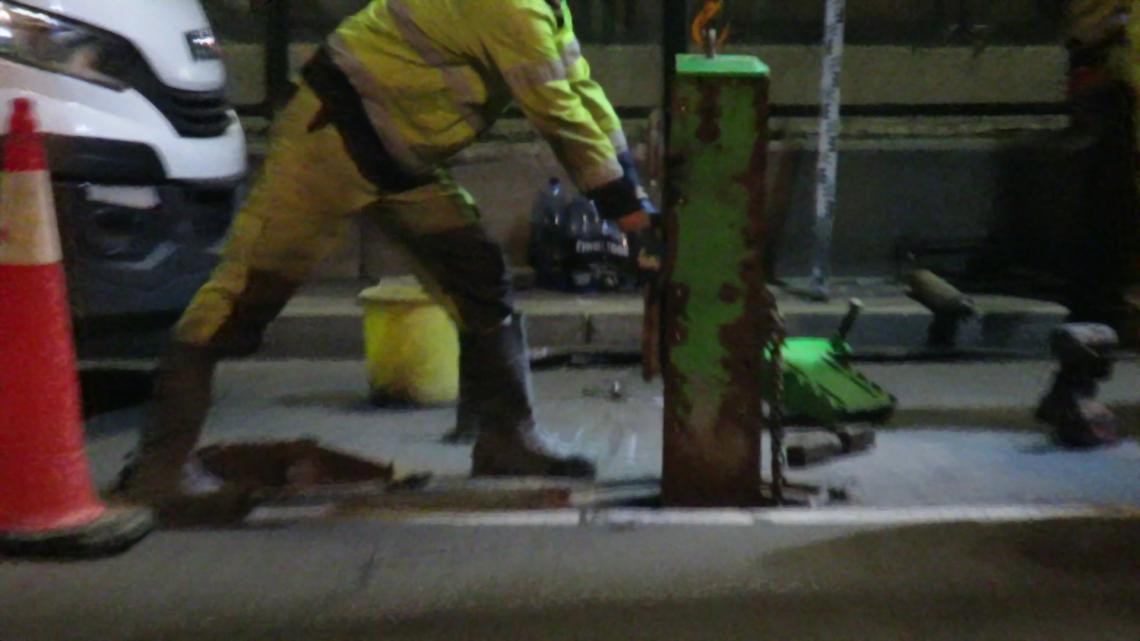
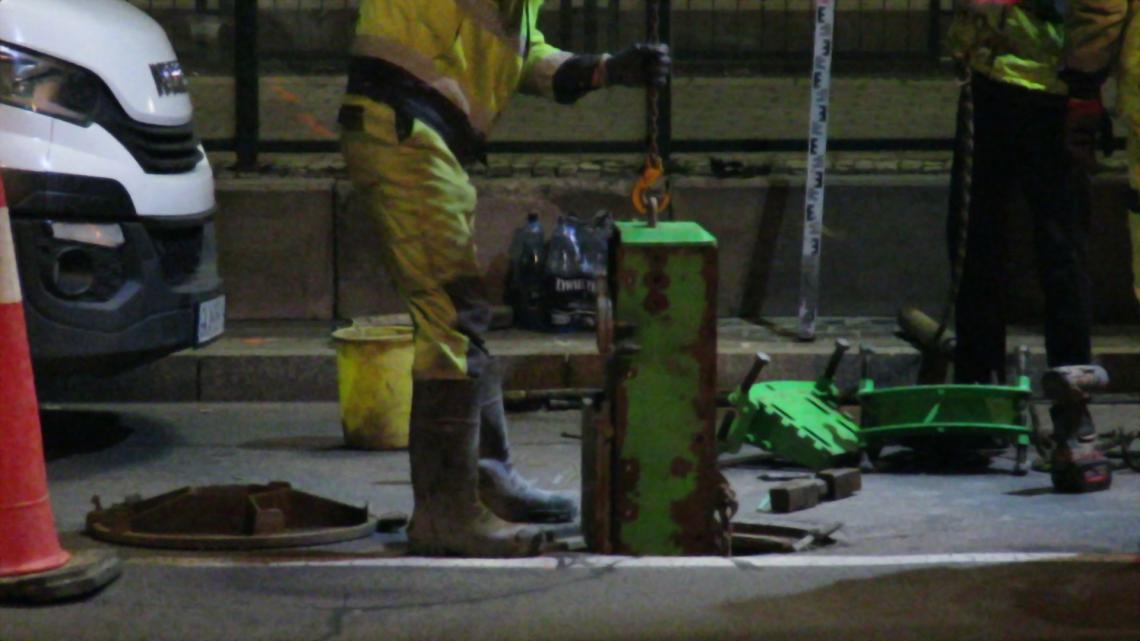
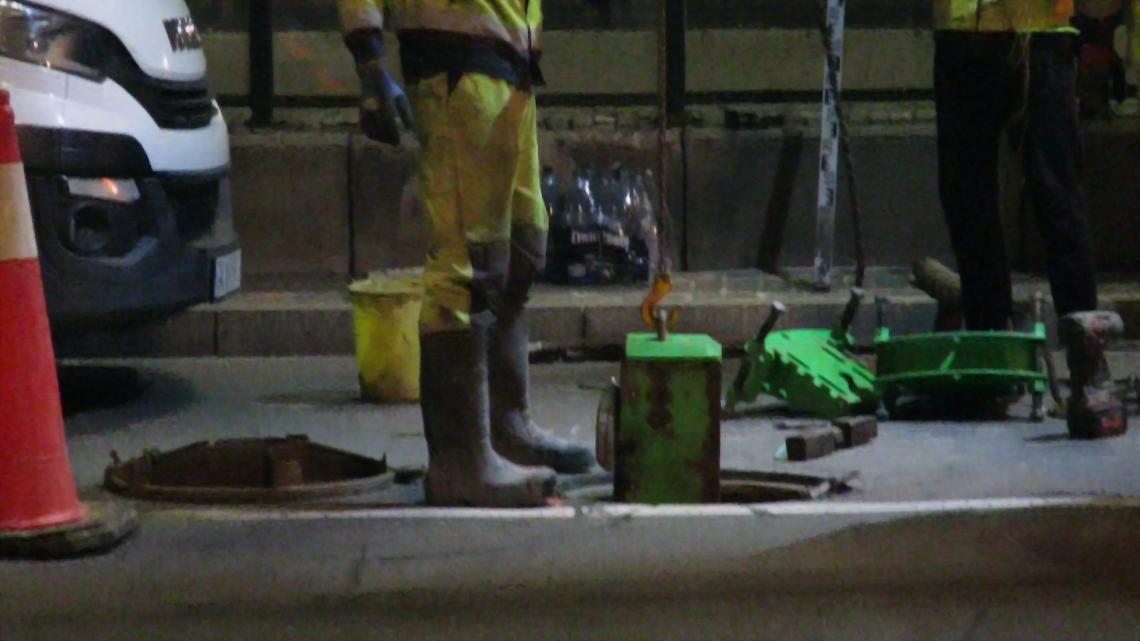
W studni startowej następuje montaż poszczególnych podzespołów wiertnicy.
Równolegle z montażem urządzeń wiertniczych dokonano stosowanych pomiarów głębokości oraz kierunku przewiertu i wyznaczono trasę przewiertu.
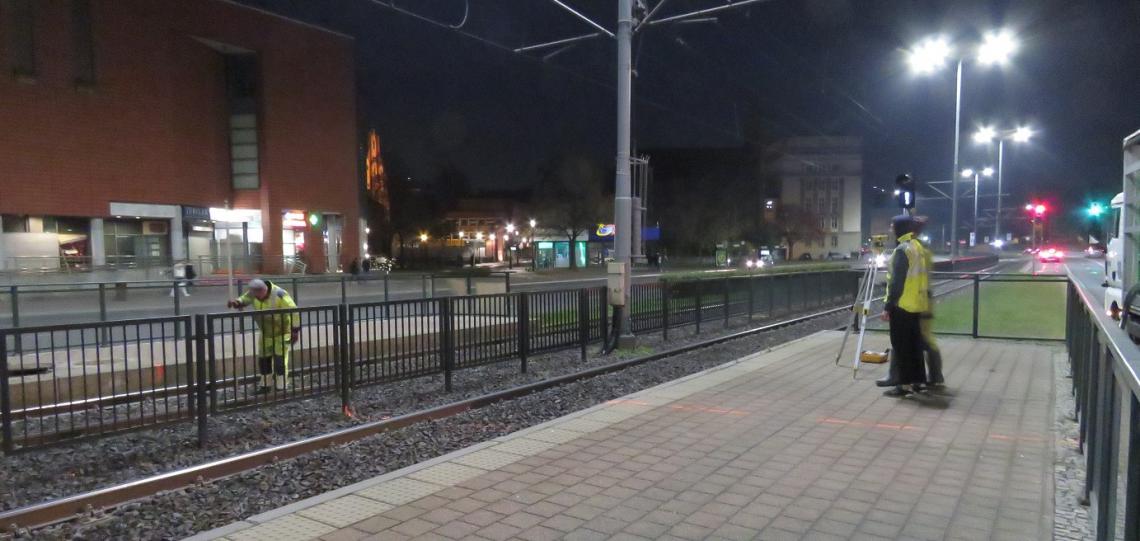
Pozostałe urządzenia związane z wiertnicą, takie jak agregat hydrauliczny zasilający oraz agregat płuczkowy znajdują się na pojeździe technicznym.
Wiertnica zostaje z nimi połączona przewodami wiertniczymi i można przystąpić do pracy.
Operator wiertnicy jest w stałym kontakcie radiowym z członkiem ekipy, odpowiedzialnym za bieżącą kontrolę trasy przewiertu. W głowicy wiercącej jest zamontowana sonda wysyłająca sygnał zawierający podstawowe elementy pozycji, takie jak chwilowy spadek grawitacyjny, głębokość na której się znajduje, położenie elementu umożliwiającego sterowanie przewiertem.
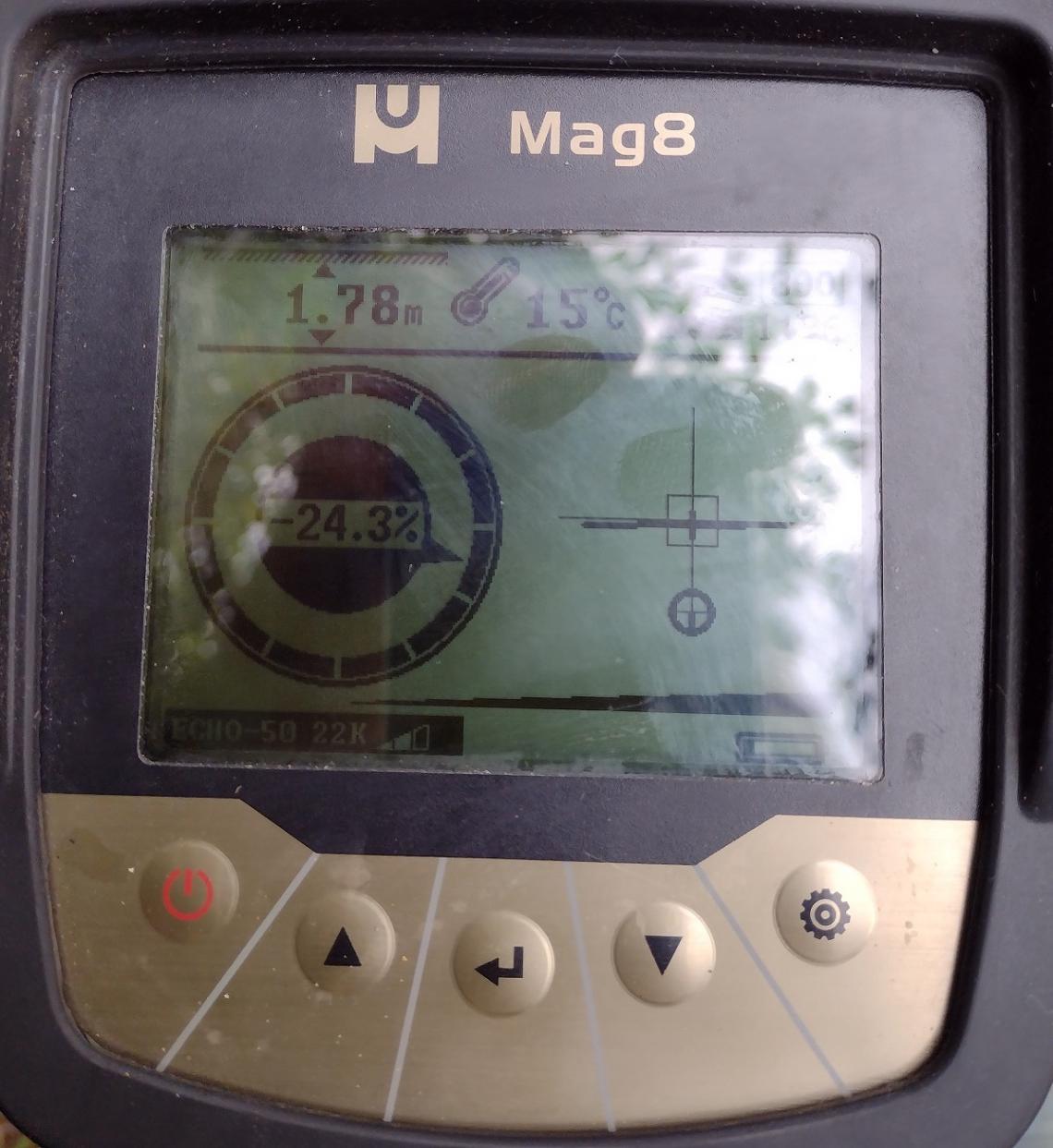
Członek ekipy czuwający nad kontrolą trasy przewiertu, przy pomocy odbiornika fal radiowych wysyłanych przez sondę, ma dostęp do wszystkich kluczowych parametrów. Informacje te na bieżąco przekazuje operatorowi wiertnicy. A ten w zależności od otrzymywanych informacji, prowadzi dalej przewiert lub dokonuje korekty trajektorii.
Sterowanie przewiertem odbywa się w identyczny sposób, jak w przypadku typowych wiertnic horyzontalnych (HDD - Horizontal Directional Drilling, czyli horyzontalne wiertnice sterowane). Na głowicy znajduje się element umożliwiający sterowanie przewiertem. W trakcie przewiertu głowica wiercąca jest pchana do przodu przy jednoczesnym ruchu obrotowym. w przypadku niepożądanej zmiany kierunku przewiertu, w odpowiednim położeniu zatrzymywany jest ruch obrotowy głowicy, przy zachowaniu jej ruchu pchającego, aż do momentu powrotu do wymaganej trajektorii. Na poniższych ilustracjach pokazano schematycznie proces sterowania przewiertem.

1 - Prowadzenie przewiertu. Trajektoria jest zgodna z oczekiwaniami czyli pchanie z jednoczesnym ruchem obrotowym
2 - Niezamierzona zmiana trajektorii przewiertu. Głowica wiercąca ucieka w górę
3 - Zatrzymanie procesu wiercenia oraz pchania

4 - Ustawienie głowicy wiercącej w położeniu umożliwiającym powrót do zadanej trajektorii
5 - Pchanie głowicy z wyłączonym ruchem obrotowym. Napór gruntu na element sterujący głowicy powoduje powrót do wymaganej trajektorii
6 - Po skorygowaniu trasy przewiertu ponowne włączenie ruchu obrotowego głowicy.
W tym miejscu warto wspomnieć, że nasza technologia poziomych przewiertów sterowanych, obejmuje dwa typy urządzeń wiercących. Mamy więc głowice wiercące z napędem pojedynczym. W tym systemie mamy jeden napęd obrotowy głowicy, odpowiadający za jednoczesne wiercenie w gruncie oraz pozycjonowanie i ewentualne korekty trajektorii. Taki typ głowicy nazywany jest głowicą z płetwą sterującą i jest ona stosowana w innych technologiach bezwykopowych, jak na przykład HDD.
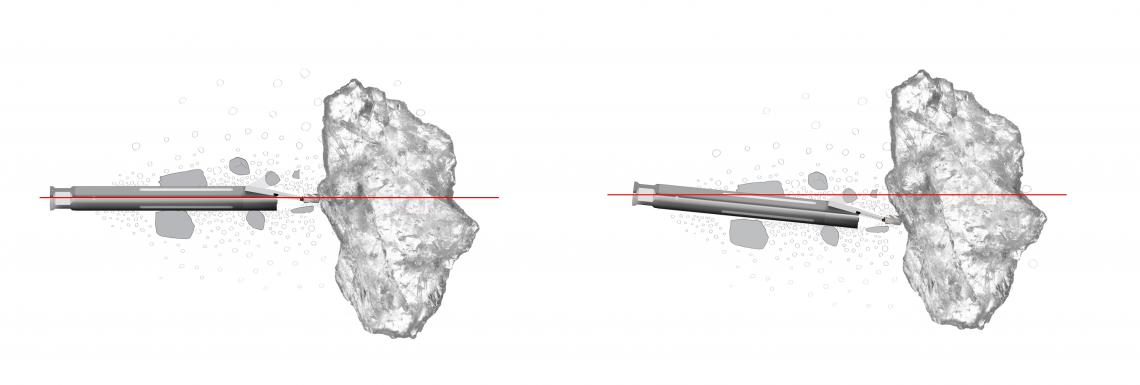
Zaletą tego rozwiązania jest prostota konstrukcji i sterowania przewiertem, co przekłada się na łatwość w realizacji budowy. Istotną jednak wadą są trudności pokonywania twardych przeszkód. Taka głowica, napotkawszy na twardą przeszkodę typu otoczak czy fragment betonowego fundamentu, nie będzie zdolna się przezeń przewiercić i zboczy z zadanego kursu. W zdecydowanej większości budów system wiercący z pojedynczym napędem w zupełności pozwala na wykonanie elementów sieci kanalizacyjnych zgodnie z projektem i wymaganym spadkiem grawitacyjnym.
Jednak w miejscach, gdzie spodziewamy się trudności warunków gruntowych, sięgamy po maszynę wiercącą z podwójnym napędem. W tej konstrukcji maszyny mamy dwa osobne napędy obrotowe: napęd wewnętrzny odpowiadający wyłącznie za wiercenie w gruncie i pokonywanie ewentualnych twardych przeszkód; oraz napęd zewnętrzny odpowiadający wyłącznie za sterowanie trasą przewiertu i ewentualne korekty kursu.
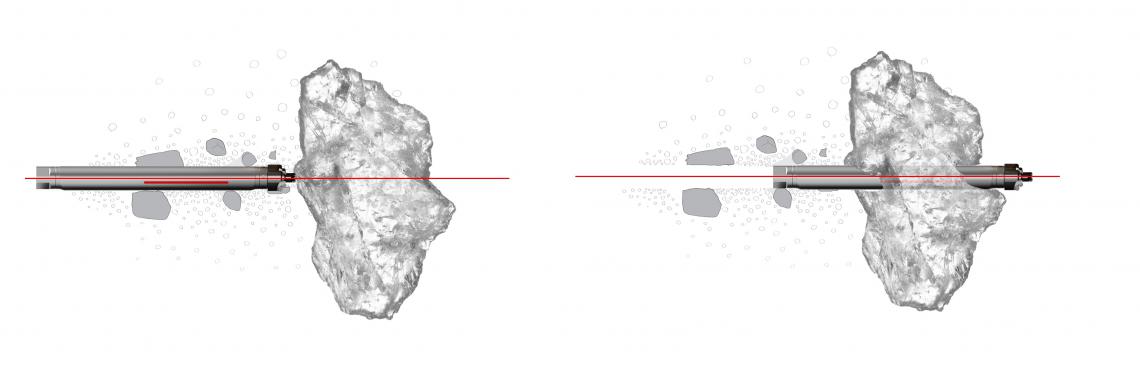
W konstrukcji napędu zewnętrznego mamy specjalną listwę sterującą, działającą analogicznie jak płetwa w napędzie pojedynczym. W przypadku niepożądanej zmiany kierunku przewiertu, zatrzymany zostaje w określonej pozycji wyłącznie napęd zewnętrzny, przy kontynuacji procesu wiercenia napędem wewnętrznym i pchania głowicy. Napęd zewnętrzny zostaje zatrzymany aż do momentu powrotu przewiertu do wymaganej trajektorii.
Wróćmy jednak do opisu renowacji sieci kanalizacyjnej przy dworcu PKP Gdańsk Główny. Operator wiertnicy znajdujący się wraz z wiertnicą w studni startowej, w porozumieniu z operatorem systemu pomiarowego, kontynuuje przewiert pilotażowy w kierunku studni końcowej. Uszkodzony kanał został uprzednio wypełniony zaczynem iniekcyjnym, więc proces wiercenia nie zostaje zakłócony napotkaniem na odmienne frakcje gruntu czy puste przestrzenie. Dodatkowo nie ma obaw, że w wyniku tąpnięcia się gruntu wokół naprawianego kanału nie dojdzie do katastrofy budowlanej.
Operator, dodając kolejne żerdzie wiertnicze, posuwa się w kierunku studni końcowej. Proces postępuje ja na schematycznych ilustracjach poniżej.

1 - Zamontowanie i uruchomienie wiertnicy
2 - Przewiert pilotażowy
3 - Zakończenie przewiertu pilotażowego w chwili osiągnięcia studni końcowej
Koniec etapu drugiego następuje w momencie przewiercenia się do studni końcowej
ETAP 3. Odbudowa uszkodzonego elementu sieci.
Przewiert pilotażowy został wykonany zgodnie z założeniami, idealnie po trajektorii zniszczonego rurociągu. Można więc było przystąpić do ostatniego etapu, czyli jego odbudowy. Zastosowano moduły rur PP 400x22.7. Dla technologii Wierceń Grawitacyjnych dedykowany jest typoszereg modułów rur PP o średnicach do 500 mm. Niemniej w zależności od wymagań inwestora technologia pozwala na zastosowanie innych typów rur wykonanych z tworzyw sztucznych, takich jak PE, PVC. Zaletą zastosowania rur PP jest bardzo wysoka gładkość ścian, wskutek czego uzyskujemy bardzo małe opory przepływu. Polipropylen cechuje się bardzo wysoką odpornością chemiczną co skutkuje niską skłonnością do zarastania wewnętrznych powierzchni przewodów kanalizacyjnych podczas spływu ścieków. Rury wykonywane z PP pracują termicznie, tzn. zmieniają swoje wymiary w zależności od temperatury. To dodatkowo sprzyja usuwaniu osadów, które w wyniku zmian wymiarów rur, pękają i są wymywane przez przepływający strumień cieczy płynącej w rurociągu. Kolejną niezwykle istotną cechą rur wykonywanych z tworzyw sztucznych PP jest ich elastyczność. W porównaniu do sztywnych tradycyjnych rur kamionkowych, rury wykonane z PP są bardziej odporne na uszkodzenia mechaniczne, rozszczelnienia instalacji, występujące na skutek naprężeń, wynikających z przemieszczania się gruntu. Niejednokrotnie wykonywaliśmy renowację sieci z rur kamionkowych, uszkodzonej właśnie na skutek przemieszczeń i tąpnięć gruntu.
Wróćmy jednak do etapu odbudowy kanalizacji. Po osiągnięciu wiertłem pilotażowym studni końcowej, przewierciliśmy się przez jej ścianę. W miejsce wiertła pilotażowego został założony rozwiertak o średnicy 420 mm, do którego przymocowano pierwszy moduł rury. Całość została następnie wciągana z powrotem w kierunku studni startowej, przy jednoczesnym rozwiercaniu zniszczonego przewodu kanalizacyjnego i dodawaniu kolejnych modułów rur. Poniższa ilustracja obrazuje kolejne elementy tego etapu.

4 - Rozwiercanie uszkodzonego rurociągu z jednoczesnym budowaniem i wciąganiem kolejnych segmentów rur modułowych
5 - Ostatnia faza budowy rurociągu, rozwiercenie ściany studni startowej
6 - Zakończony proces odbudowy sieci. Uszczelnienie łączenia rury ze ścianami studni
Kolejną istotną cechą stosowanych przez nas standardowo modułów rurowych jest bardzo mała wymagana przestrzeń do ich montażu. Łączenie kolejnych modułów odbywa się przy pomocy małej, kompaktowej ściskarki hydraulicznej. Proces budowy rurociągu z modułów rur może odbywać się w obszarze ograniczonym średnicą studni o wymiarach DN 1000. Typowa długość brutto modułu wynosi 700 mm.
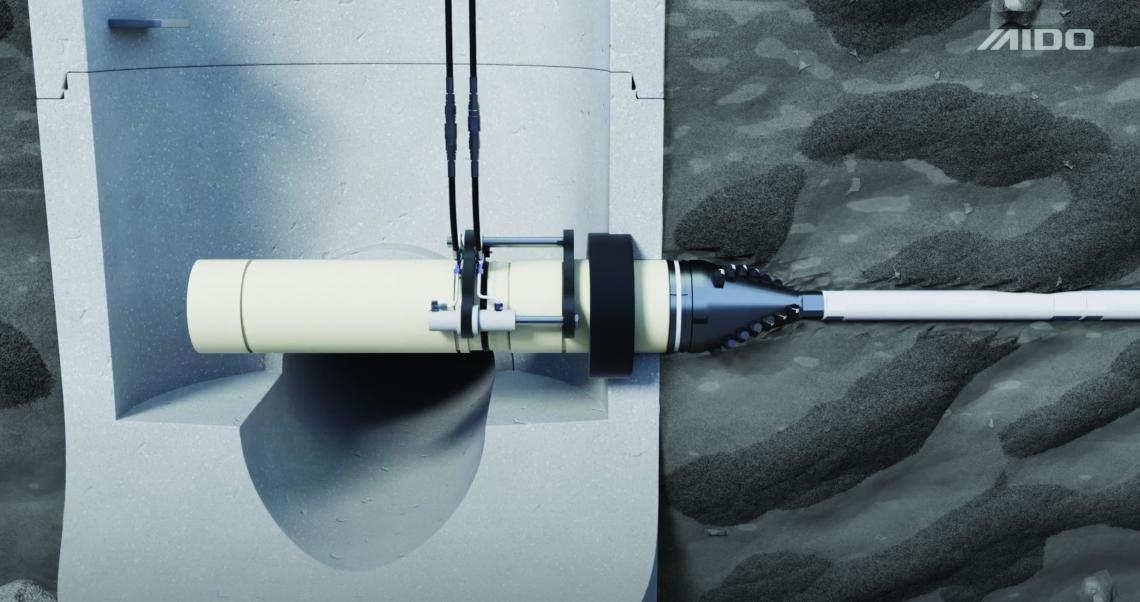
W studni startowej operator wiertnicy wciąga rurociąg demontując kolejne segmenty żerdzi wiertniczych
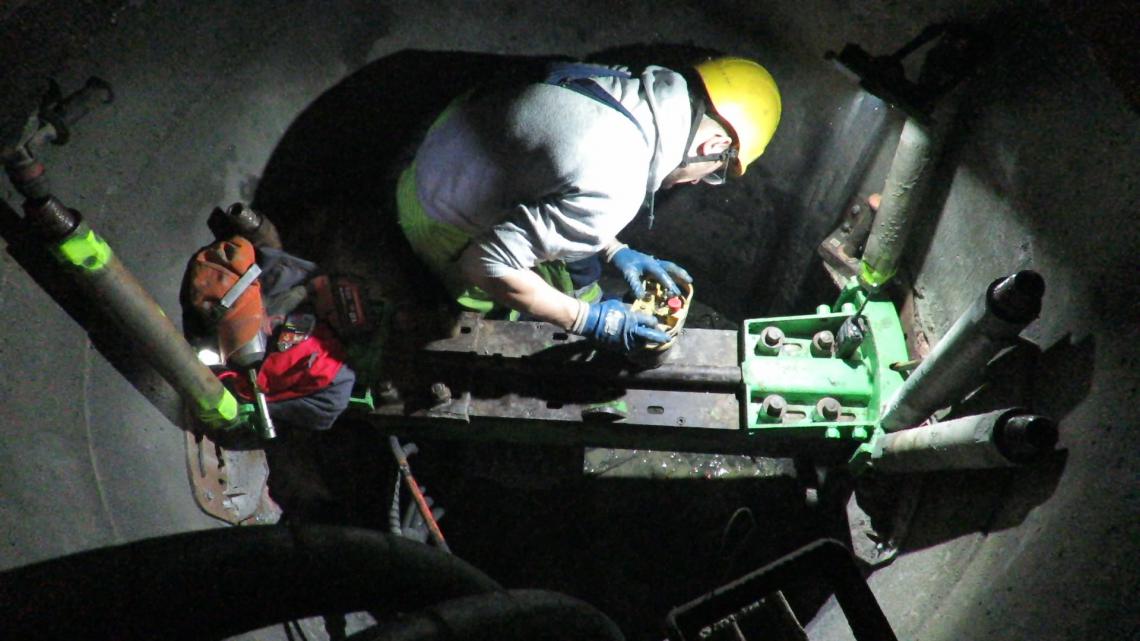
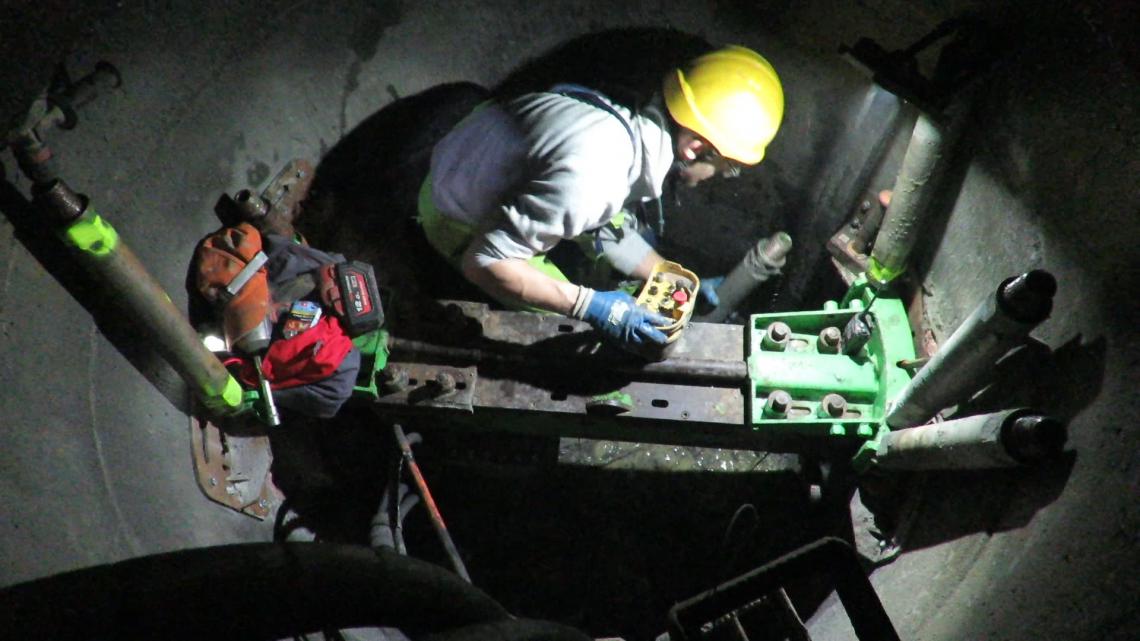
W studni końcowej przy pomocy ściskarki hydraulicznej łączone są kolejne moduły rur PP z jednoczesnym wciąganiem już zbudowanego odcinka w kierunku studni startowej.
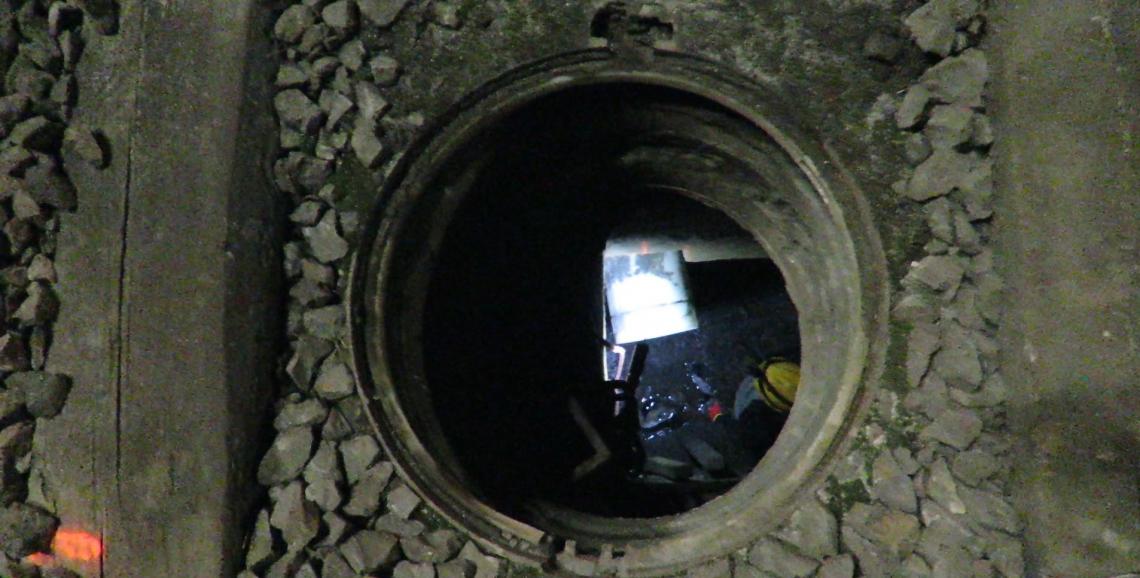
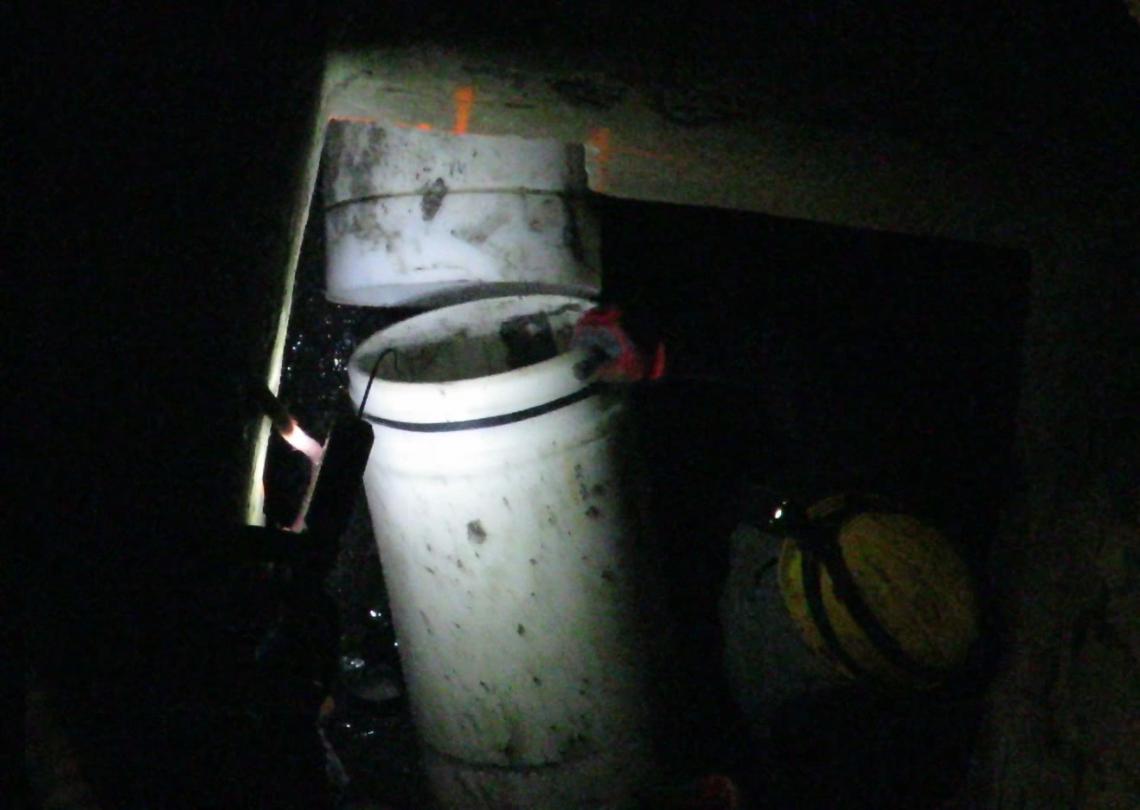
Ostatnią czynnością było sprawdzenie jakości wykonania odbudowanego rurociągu oraz zgodności z wymaganym spadkiem grawitacyjnym, przy pomocy specjalistycznego systemu wizyjnego CCTV.
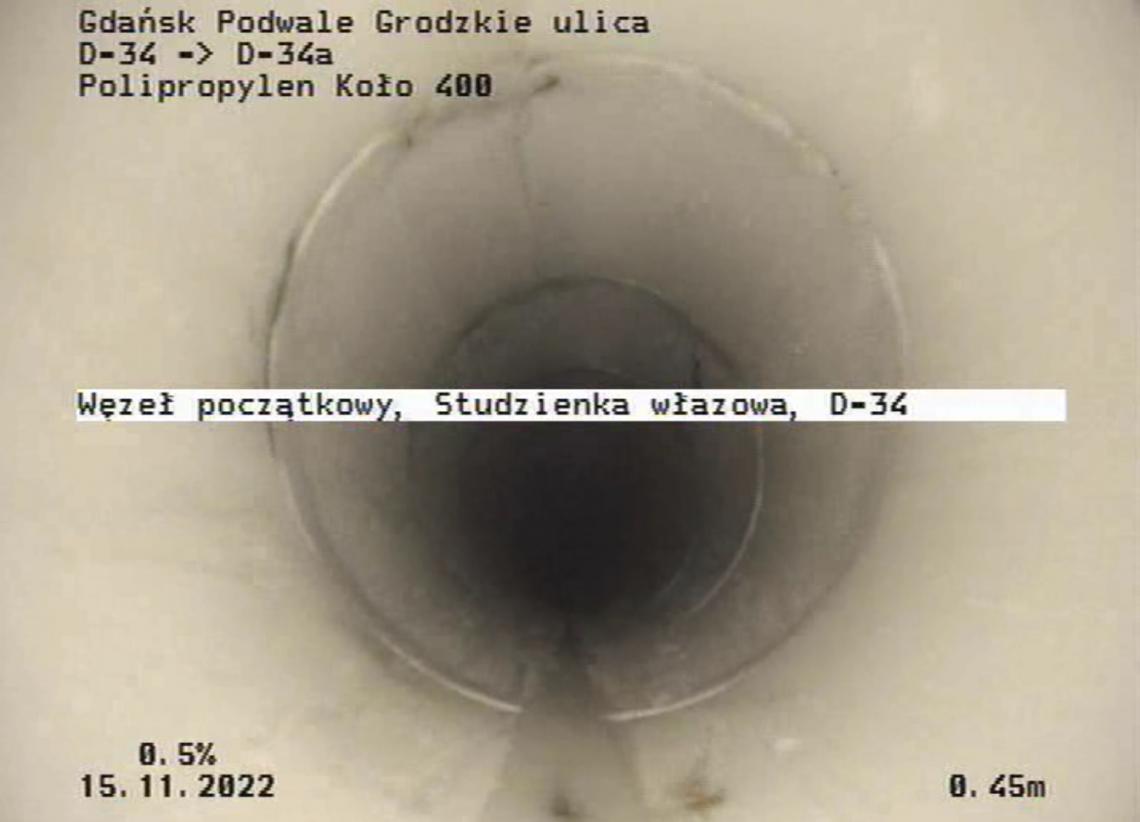
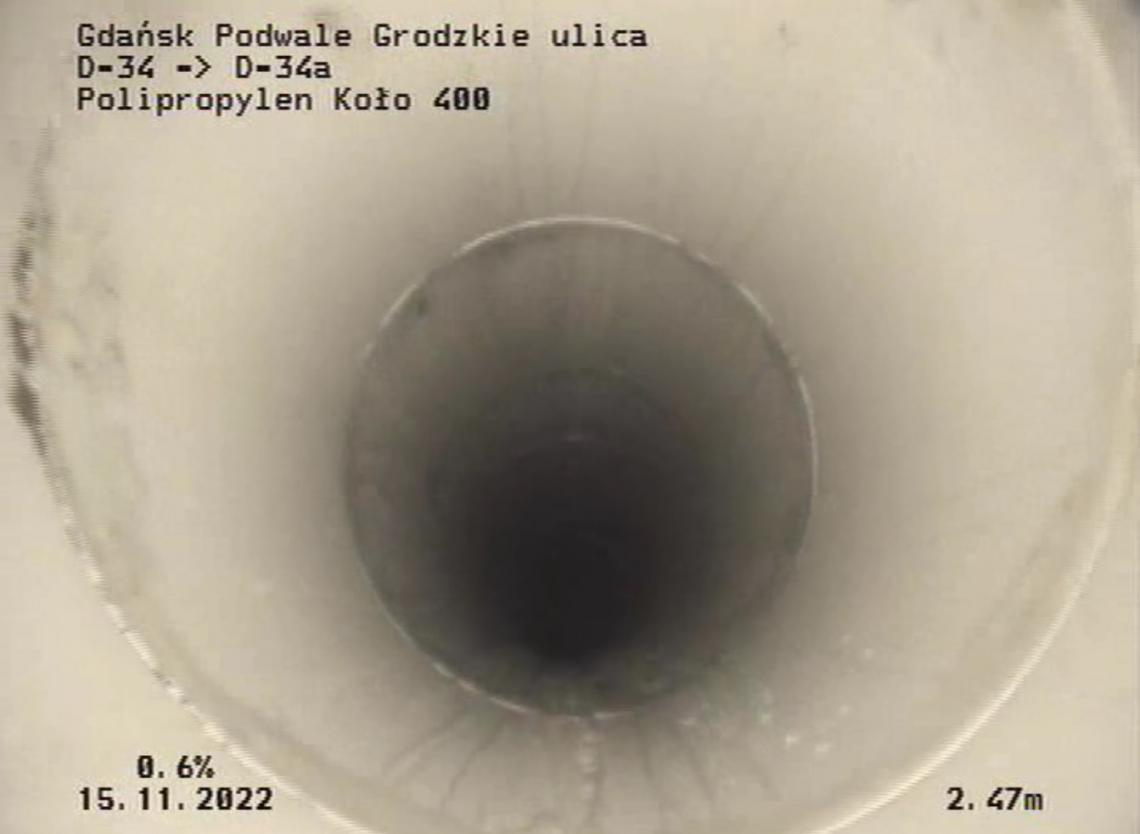
Zleceniodawca dokonał odbioru prac nie wnosząc żadnych uwag.
Warto przeczytać także o naszych innych wybranych realizacjach:
